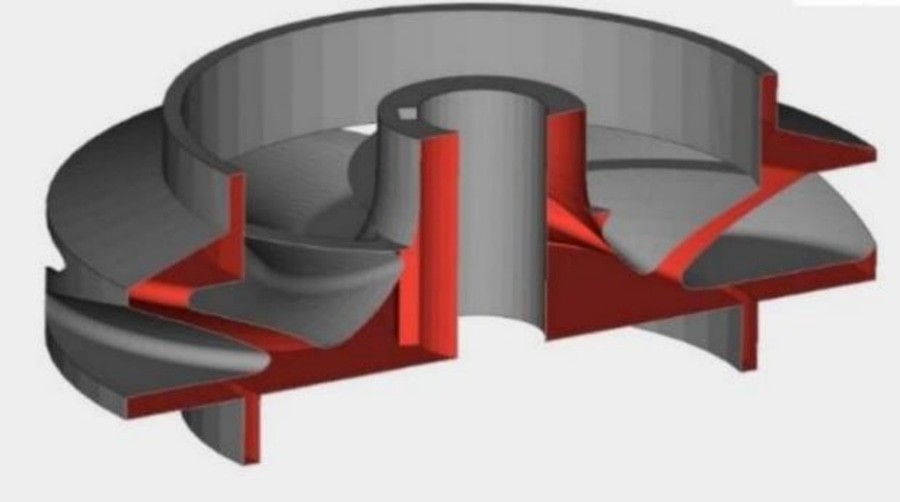
Vedi traduzione automatica
Questa è una traduzione automatica. Per vedere il testo originale in inglese cliccare qui
#White Papers
{{{sourceTextContent.title}}}
Studio della produzione di una girante chiusa in acciaio inox 316L con la macchina per la fusione a letto di polvere laser Eplus3D
{{{sourceTextContent.subTitle}}}
Notizie aziendali
{{{sourceTextContent.description}}}
Yousef Alhorr1, Qusai Alkhalaf 2*
1Dottorato di ricerca, presidente dell'Organizzazione del Golfo per la ricerca e lo sviluppo (GORD), QSTP, Doha, Qatar
2PhD, responsabile delle operazioni del centro di produzione additiva. Organizzazione del Golfo per la Ricerca e lo Sviluppo (GORD-3D), QSTP, Doha, Qatar
Abstract: La produzione di giranti chiuse tramite la tecnologia Laser Powder Bed Fusion comporta complessità intrinseche, richiedendo un'attenzione meticolosa alla progettazione della struttura di supporto, alla determinazione dell'angolo di costruzione e alla densità energetica della pelle per garantire una produzione di successo. Questo studio esplora l'uso dell'acciaio inossidabile 316L nella fabbricazione di giranti chiuse con la tecnologia LPBF. L'obiettivo è quello di analizzare l'impatto dei parametri di processo e degli angoli di costruzione sulla qualità della fabbricazione delle giranti. Inoltre, si studia l'effetto della densità di energia sui valori di rugosità superficiale e durezza della girante. L'indagine esamina angoli di costruzione di 0˚, 30˚ e 90˚ per una girante chiusa, rivelando che un angolo di costruzione di 30˚ produce parti stampate di successo. Inoltre, per ottenere giranti chiuse senza difetti, è indispensabile mantenere la densità di energia verso il basso tra l'80% e il 100% della densità di energia verso l'interno. La durezza massima e la rugosità superficiale minima sono state registrate rispettivamente a 233 HV e 12,79 µm, quando la densità di energia era rispettivamente di 41,66 J/mm³ e 55,55 J/mm³. La novità di questo studio consiste nella fabbricazione di giranti chiuse in acciaio inox 316L mediante fusione laser a letto di polvere.
Parole chiave: produzione additiva; fusione laser a letto di polvere (LPBF); girante chiusa; fusione laser selettiva (SLM)
1. Introduzione
La girante costituisce un elemento indispensabile nei sistemi di pompaggio, svolgendo un ruolo centrale nel determinare la capacità idraulica e l'efficienza della portata nelle turbomacchine [1]. Distinta in quattro classi geometriche, ossia giranti aperte, chiuse, semiaperte e a vite, la girante chiusa (CI) si distingue per essere particolarmente impegnativa da produrre a causa delle intricate caratteristiche interne. I metodi tradizionali prevedono l'assemblaggio di CI in segmenti, come il mantello, il mozzo e le pale, utilizzando tecniche di giunzione come la saldatura, la brasatura o la rivettatura. Tuttavia, questi approcci introducono difetti e distorsioni, rivelandosi inadeguati per applicazioni esigenti e ad alte prestazioni. Di conseguenza, l'adozione di CI in un unico pezzo diventa imperativa, con tecniche di produzione come la microfusione, la fresatura integrale e la lavorazione a scarica di elettroni (EDM) che sono specializzate ma che richiedono tempo, manodopera qualificata e impostazioni specializzate, con conseguente aumento dei costi di produzione complessivi [2].
Per far fronte a queste sfide, l'Additive Manufacturing (AM) si presenta come una soluzione trasformativa per la CI a pezzo singolo, offrendo la prospettiva di ridurre le incertezze sui tempi di consegna e di aumentare la flessibilità della progettazione [3,4]. La Laser Powder Bed Fusion (LPBF), una delle principali tecnologie AM, fonde selettivamente la polvere strato per strato utilizzando un laser, consentendo così la produzione di parti dalla forma complessa con un'alta risoluzione di circa 50 micrometri [6-9]. La LPBF ha dimostrato un notevole successo nella stampa di parti complesse da una serie di materiali metallici, tra cui acciai, leghe di nichel, leghe di titanio e leghe di Inconel [10-11].
Anche se tecnologie alternative come il metodo di deposizione fusa (FDM) possono essere utilizzate per la stampa di giranti, la loro idoneità è generalmente limitata ad applicazioni meno complesse [12]. Al contrario, l'LPBF con stampa su metallo è indispensabile per ottenere funzionalità ad alte prestazioni [13]. Numerosi studi sottolineano il successo dell'applicazione di LPBF nella stampa di giranti aperte, comprendendo indagini sulle proprietà dei materiali, previsioni sulla storia termica e ottimizzazione dei parametri di processo [14-16]. È significativo che la LPBF consenta la fabbricazione di giranti con materiali riciclati, accentuando il suo potenziale per le pratiche di produzione sostenibili [17]. Nonostante questi progressi, le sfide persistenti riguardano l'ottenimento di stampe 3D precise e prive di difetti. La deformazione geometrica, esemplificata da macchie scure e legami metallurgici non ottimali tra gli strati, contribuisce a problemi di varia natura, tra cui guasti geometrici, imprecisioni dimensionali, strutture incomplete e impedimenti nel processo di stampa [27]. Inoltre, i difetti di detriti, derivanti dalla pressione di rinculo del vapore metallico durante la stampa, provocano il distacco della polvere non fusa o del metallo fuso e influenzano lo stato di fusione degli strati successivi, compromettendo in ultima analisi la resistenza alla trazione e le prestazioni a fatica della parte stampata [28-29].
L'acciaio inossidabile è ampiamente considerato un'opzione eccellente per la stampa laser a fusione a letto di polvere. Una girante chiusa in acciaio inossidabile ha numerose applicazioni, ad esempio nei sistemi di acque reflue. Le preoccupazioni principali per la stampa dell'acciaio inossidabile riguardano la gestione della densità di energia e l'ottimizzazione dell'angolo del materiale di supporto. Questa metrica racchiude l'energia immessa per unità di volume durante il processo di fusione dello strato. In particolare, la densità di energia è definita come:
Nell'equazione, P (W) rappresenta la potenza del laser, v indica la velocità di scansione (mm/s), h (μm) indica la distanza del tratteggio, z (μm) indica lo spessore dello strato, Livelli di energia bassi portano a una porosità da mancata fusione, indicando un'energia insufficiente per la completa fusione della polvere e risultando in porosità irregolari diffuse in tutto il pezzo [31]. Valori di densità ad alta energia causano una sovra-fusione, spesso definita porosità a buco di serratura [32-34]. In questo stato, le piste fuse si frammentano, causando una solidificazione non uniforme e difetti finali del pezzo. La regione stabile garantisce la fusione completa delle piste e l'adesione degli strati entro i limiti della densità di energia. La complessità della stampa della girante è fondamentale nella fusione laser a letto di polvere, con metalli comuni quali Inconel 625 e Inconel 718.
Per quanto a conoscenza degli autori, esiste una notevole assenza di indagini sull'applicazione dell'acciaio inossidabile 316L nella stampa di giranti chiuse mediante fusione laser a letto di polvere. La presente ricerca si propone quindi di colmare questa lacuna, intraprendendo la produzione di una girante chiusa mediante fusione laser a letto di polvere. Il nostro obiettivo principale è quello di analizzare l'impatto di variabili quali il materiale di supporto, l'angolo di costruzione e la densità di energia della pelle sul processo di fabbricazione della girante chiusa. Inoltre, intendiamo studiare l'effetto della densità di energia sulla rugosità e sulla durezza della superficie.
2. Metodo e lavoro sperimentale
Il metodo e il lavoro sperimentale applicato per studiare l'angolo della struttura di supporto e le proprietà meccaniche finali della girante sono illustrati nella Figura 1. Il metodo è suddiviso in tre fasi. Il metodo è suddiviso in tre fasi. La prima fase prevede la selezione dell'angolo appropriato della struttura di supporto tra 0°, 30° e 90°. Una volta determinato l'angolo ottimizzato, si esamina la tessitura della microstruttura mediante scansione al SEM per la fase 2. La terza fase si concentra sull'esame dell'effetto della densità di energia sulla rugosità e sulla durezza.
2.1 Progettazione della girante
Sono state progettate due giranti chiuse di dimensioni diverse: una con un diametro di 145 mm e l'altra con un diametro di 100 mm. La girante è divisa in tre sezioni principali lungo la sua direzione di costruzione: la base, la sezione centrale e la sezione delle alette. Queste sezioni hanno strutture complesse, tra cui diverse geometrie di alette sottili inclinate, che rendono la produzione un processo impegnativo. Poiché la sezione trasversale cambia lungo l'altezza della girante, l'area scansionata dal laser varia da strato a strato. La struttura della girante è illustrata nella Figura 2.
2.2 Angolo di costruzione e struttura di supporto per giranti chiuse
Per determinare l'angolo di costruzione ottimale per una girante chiusa all'interno della camera di costruzione della macchina LPBF, sono stati selezionati tre angoli comuni (90°, 30° e 0°) per valutarne l'impatto sul processo di produzione. La scelta dei supporti dipende dalla forma della girante: sono stati scelti supporti a forma di blocco, come illustrato nella Figura 3. Numerosi studi hanno dimostrato che l'impiego di supporti solidi o a blocco consente di migliorare le caratteristiche meccaniche dei campioni e la finitura superficiale, soprattutto per le superfici sporgenti. Questi supporti facilitano un'efficace dissipazione del calore, ottimizzando così i risultati. La Figura 4 illustra la vista del supporto a blocchi, con l'aggiunta di supporti ad albero per facilitare la rimozione. Il software utilizzato per la preparazione della costruzione è stato MaterialsMagic per la preparazione dei supporti e SolidWorks per la progettazione.
2.3 Elaborazione di LPBF
Le giranti sono state prodotte con una macchina Eplus3D EP-M260 LPBF, utilizzando materiale in acciaio inox 316L. La Eplus3D M260 si trova presso il Centro 3D della Gulf Organisation for Research & Development (GORD 3D). La vista attuale della macchina Eplus3D è mostrata nella Figura 5. Le giranti sono state progettate con diametri di 145 mm e 100 mm. La stampa di una girante di 145 mm di diametro con un angolo di costruzione di 90° richiede circa 103 ore e 4.393 strati con uno spessore di 30 µm. Una girante di 145 mm di diametro stampata con un angolo di costruzione di 30˚ richiede 53 ore, con 3.124 strati. Una girante di 100 mm di diametro stampata con un angolo di costruzione di 0˚ richiede circa 38 ore, con 1.833 strati.
La selezione dei parametri per la stampa di giranti chiuse è cruciale, e la densità di energia è una considerazione particolarmente importante. Il down-skin si trova nei primi tre strati sopra il materiale di supporto, che può potenzialmente danneggiare il pezzo durante il processo di stampa. Pertanto, la scelta della densità di energia del down-skin è essenziale, in quanto funge da ponte tra il materiale di supporto e il nucleo della girante. La densità di energia in- skin, invece, riguarda il nucleo della girante. Secondo la revisione della letteratura, la densità di energia down-skin dovrebbe essere idealmente compresa tra il 50% e l'80% della densità di energia in-skin. Nel presente studio, sono stati considerati due casi per la densità di energia del down-skin: uno in cui la densità di energia del down-skin è uguale a quella dell'in-skin, e un altro in cui la densità di energia del down-skin è impostata al 20% della densità di energia dell'in-skin. La figura 6 illustra la visione attuale del processo di stampa. La Tabella 2 fornisce i dettagli dei parametri di processo con queste variazioni di densità energetica per ogni fase.
2.4 Test di durezza
Le prove di microdurezza Vickers sono state eseguite secondo lo standard ASTM E92-17 utilizzando una macchina per prove di microdurezza Vickers. Un penetratore piramidale con punta di diamante ha applicato una forza specifica (300 gf, 2,94 N) alla superficie del campione per 10 secondi per ogni indentazione. Su ogni campione sono state effettuate tre indentature, escludendo quelle all'interno dei pori. Il valore di durezza Vickers (HV) è stato determinato misurando le diagonali di ciascuna indentatura a forma di diamante, facendo la media con il software della macchina. la media di queste misure è stata considerata la durezza del campione.
2.5 Preparazione della superficie e caratterizzazione microstrutturale
Con la girante è stato prodotto un campione di 5 mm di spessore. I campioni sono stati sottoposti ad abrasione con dischi abrasivi al carburo di silicio di varie grane (200, 600, 800 e 1200). I campioni lavorati sono stati poi esaminati al microscopio ottico per studiare le caratteristiche microstrutturali, tra cui la polvere non fusa e i difetti. Successivamente, sono stati analizzati con un SEM Phenom ProX Desktop per studiare la sottostruttura e la morfologia.
3. Risultati e discussione
3.1 Influenza dell'angolo di costruzione sulla costruzione della girante
Le strutture di supporto giocano un ruolo fondamentale nel dissipare il calore dal bagno di fusione, nel ridurre le sollecitazioni termiche e nel controbilanciare la forza della lama di ricopertura, che esercita una pressione dinamica contro il bordo d'attacco dello strato. La conduzione del calore varia in base alla densità relativa; è significativamente più bassa negli strati di polvere con densità di impaccamento inferiori rispetto alle strutture a supporto solido. Le diverse strutture di supporto dissipano il calore a vari livelli; tuttavia, una maggiore dissipazione di calore, come nel caso dei supporti a blocchi, rende più difficile la rimozione. I supporti solidi/blocchi consentono di ottenere proprietà meccaniche e finiture superficiali superiori sulle superfici sporgenti, anche se con un aumento dei materiali, dei tempi di stampa e dei costi di post-lavorazione. Oltre alla dissipazione del calore, le strutture di supporto sostengono i pezzi e contrastano le forze di trazione durante il raffreddamento rapido, riducendo i rischi di deformazione e delaminazione. Un supporto insufficiente per le superfici rivolte verso il basso comporta problemi di forma e precisione dimensionale. Pertanto, la selezione dei parametri per gli strati di supporto e di rivestimento è fondamentale per attenuare le tensioni interne e la delaminazione. È fondamentale accertare un "angolo di costruzione affidabile", ovvero l'angolo minimo che garantisce la produzione del pezzo senza formazione di scorie e distacchi.
Come descritto nella sezione metodi, la girante è stata esaminata con tre angoli di costruzione durante la costruzione: 90°, 30° e 0°. Nel caso di CI-A, si è verificato un significativo cedimento della girante, attribuito alla debolezza delle strutture di supporto scelte prima del processo, come illustrato nella Figura 7. La combinazione di supporto a blocco e supporto ad albero si è rivelata inadeguata a sostenere il peso della girante, portando alla deformazione della struttura di supporto, particolarmente evidente a un angolo di costruzione di 90°. La deformazione osservata può essere attribuita al peso significativo esercitato dalla parte costruita e dalla ricopertura durante il processo di stampa. Il recoater, in particolare, svolge un ruolo fondamentale nel processo di stratificazione, diffondendo la polvere sul letto di costruzione. Tuttavia, questa azione ripetitiva, soprattutto durante l'applicazione degli strati successivi, può esercitare una forza eccessiva, con conseguenti danni, soprattutto in corrispondenza degli angoli di 90°, dove i bordi della parte stampata sono intrinsecamente più deboli.
Nei casi di CI-B e CI-C, si è osservato un successo nella costruzione della girante con meno difetti. La produzione di una girante più piccola e più grande con un angolo di costruzione di 30° riduce notevolmente i difetti e i danni durante il processo di fabbricazione, mostrando risultati superiori rispetto ai casi in cui l'angolo di costruzione è impostato a 90°. Questo fenomeno è chiaramente mostrato nella Figura 8. Non si sono verificati danni grazie all'angolo di costruzione di 30°, che ha ridotto il peso della parte stampata e migliorato le prestazioni del recoater. Con un angolo di 30°, il recoater entra in contatto con meno polvere lungo i bordi rispetto agli angoli di 90° e 0° durante ogni movimento di spalmatura. Il successo dell'orientamento a 30° è attribuito a diversi fattori chiave. In primo luogo, la transizione graduale in sezione trasversale dai supporti alle parti solide all'interno di ogni strato ha ridotto al minimo le concentrazioni di stress e i potenziali difetti, distinguendosi da orientamenti come 0 gradi in cui si verificano cambiamenti bruschi. In secondo luogo, l'assenza di supporti solidi, tipicamente richiesti per le sporgenze in orientamenti come i 90 gradi, ha contribuito in modo significativo al successo dell'orientamento a 30 gradi. L'eliminazione dei supporti non solo ha semplificato il processo di stampa, ma ha anche attenuato le sfide associate alla post-elaborazione e alle imperfezioni superficiali, migliorando in definitiva la qualità e l'integrità strutturale dei pezzi. Inoltre, è stato osservato che i pezzi stampati con un orientamento di 30 gradi hanno mostrato un peso ridotto rispetto a quelli stampati a 90 gradi. Questa riduzione di peso, vantaggiosa in varie applicazioni, ha ulteriormente sottolineato l'efficacia dell'orientamento a 30 gradi. Nel complesso, questi risultati evidenziano i molteplici vantaggi dell'orientamento a 30 gradi nella produzione additiva, offrendo spunti preziosi per ottimizzare le strategie di orientamento nelle applicazioni future.
Nel caso del CI-D, quando la girante chiusa è piccola, il fallimento si è verificato quando l'angolo di costruzione era di 0˚ . Nonostante le dimensioni ridotte dell'IC, il cedimento a questo angolo non è dovuto alle sue dimensioni, ma piuttosto alla debolezza della struttura di supporto, come illustrato nella Figura 9. Inoltre, l'uso di un'elevata velocità di rotazione della girante ha permesso di ottimizzare le strategie di orientamento nelle applicazioni future. Inoltre, l'uso di un'elevata velocità di scansione di 900 mm/s ha provocato l'accumulo di detriti sulla superficie della ventola, come illustrato nella Figura 9. Inoltre, sono stati osservati danni lungo il bordo, causati dalle impostazioni ad alta potenza in queste regioni.
3.2 Impatto dei parametri del Down-Skin sulla costruzione della girante chiusa
Il down-skin indica tipicamente gli strati, da 1 a 4, posizionati sopra i supporti o direttamente sulla polvere. Di solito, tre strati sono identificati come down-skin e richiedono parametri di lavorazione diversi rispetto agli strati "in-skin" o "core". I parametri relativi al down-skin, come la velocità e la potenza di scansione, sono considerati critici per la costruzione di qualsiasi pezzo che utilizzi la tecnologia di fusione laser a letto di polvere. Quando la densità di energia del down-skin rappresenta solo il 20% della densità di energia dell'in-skin, si verificano danni evidenti sul pezzo. Anche nei casi in cui non si osservano danni, sulla superficie della girante chiusa si manifestano segni di bruciatura e difetti, particolarmente evidenti nelle giranti chiuse più grandi, come la CI-A, come illustrato nella Figura 7. Ciò sottolinea l'importanza di due fattori primari che contribuiscono al cedimento del pezzo: l'inadeguatezza della struttura di supporto e l'insufficiente densità energetica del down-skin, che misura 12,15 J/mm³.
Man mano che il diametro della girante diminuisce, come nel caso di una girante di 100 mm di diametro, l'impatto del down-skin diminuisce, in particolare con un angolo di costruzione di 30˚ . Nonostante la densità di energia del down-skin rappresenti solo il 20% della densità di energia dell'in-skin, si possono comunque osservare lievi bruciature in aree specifiche della parte stampata, come illustrato nella Figura 10. Inoltre, aumentando il diametro della girante, l'impatto del down-skin diminuisce. Inoltre, l'aumento del diametro della girante aumenta la probabilità di danneggiamento del pezzo. Tuttavia, l'allineamento della densità di energia verso il basso con la densità di energia verso l'interno con un angolo di 30° garantisce la stampa della girante senza difetti, come illustrato nella Figura 10.
La densità di energia verso il basso è un parametro cruciale nel processo di costruzione del pezzo, determinato dalla complessità e dalle dimensioni del pezzo. Nelle parti più piccole, il suo impatto è meno pronunciato rispetto a quelle più grandi. Per ottenere pezzi privi di difetti, la densità di energia verso il basso dovrebbe essere idealmente compresa tra l'80 e il 100% della densità di energia verso l'interno.
3.3 Effetto della densità di energia volumetrica (VED) sulla microstruttura della girante
La girante stampata con una densità di energia di 35 J/mm³, considerata bassa, mostra una mancanza di fusione attribuita all'elevata velocità di scansione, che non consente al laser di fondere la polvere, come illustrato nella Figura 11. Aumentando la densità di energia a 55,55 J/mm³, questi problemi di mancata fusione e di mancanza di adesivo sono diminuiti grazie alla densità di energia ottimale, che consente alla polvere di fondersi correttamente, come illustrato nella Figura 12.
3.4 Influenza della VED sulla durezza
Le misure di durezza Vickers dei campioni stampati variavano approssimativamente da 226 a 233 HV. Due campioni, caratterizzati da una densità di energia volumetrica (VED) di 40 J/mm³, hanno mostrato valori di durezza inferiori a 230 HV. In particolare, i campioni CI-C-1e CI-C-2, con densità di energia rispettivamente di 33,33 J/mm³ e 37,037 J/mm³. La maggior parte dei campioni rientrava nell'intervallo tra 220 e 230 HV, come mostrato nella tabella 3. In particolare, il campione CI-C-3, con una VED di 41,66 J/mm³, ha mostrato la durezza più elevata, pari a 233 HV.
I valori di durezza Vickers (HV) ottenuti sono paragonabili a quelli dei pezzi in 316L prodotti per colata, che in genere presentano una durezza di 210 HV. Tuttavia, i valori rimanenti erano superiori a questo parametro di riferimento. È stato osservato che quanto più un campione è poroso, tanto più bassa è la sua durezza, poiché la presenza di pori permette alle indentazioni di penetrare più profondamente, dando luogo a indentazioni più grandi e di conseguenza a valori di HV più bassi. In questo esperimento, si è cercato intenzionalmente di evitare i pori superficiali durante ogni indentazione, con il risultato di una correlazione minima tra durezza e porosità superficiale.
3.5 Rugosità della superficie
La rugosità superficiale è un parametro importante nella fusione laser a letto di polvere, influenzato dalla densità di energia. L'aumento della densità di energia porta in genere a una riduzione della rugosità media del pezzo. Questa riduzione si verifica perché una maggiore densità di energia consente un'esposizione più prolungata ad alta energia e bassa velocità, facilitando una migliore fusione della polvere durante il processo. Inoltre, la diminuzione della velocità di scansione aumenta la densità di energia, riducendo di conseguenza l'effetto balling durante la lavorazione, contribuendo ulteriormente alla riduzione della rugosità superficiale. Ad esempio, nella Figura 13, la massima rugosità superficiale si osserva a 13,82 µm quando la densità di energia è bassa. Tuttavia, aumentando la densità di energia a 55 J/mm3 si ottiene una diminuzione della rugosità superficiale a 12,79 µm.
3.6 Confronto con lo studio precedente
I risultati sono stati confrontati con la letteratura basata sulla prova di durezza, in particolare con quelli di Eliasu et al[35]. Per quanto riguarda le proprietà meccaniche, abbiamo osservato piccole differenze nella prova di durezza rispetto a Eliasu et al[35], con una variazione del valore dell'intervallo tra 2 e 5 HV, come indicato nella Tabella 4. Confrontando la microstruttura, si nota che la microstruttura di Eliasu et al. [35] è migliore del nostro risultato attuale, il che potrebbe aver causato i cambiamenti osservati nella durezza, come illustrato in figura17.
4. Conclusioni
La stampa di una girante chiusa tramite fusione laser a letto di polvere richiede un'attenta considerazione dei parametri di stampa per mitigare le complessità associate al processo di stampa. Questi includono una progettazione sottile per la selezione corretta dell'angolo di costruzione e l'uso di un'adeguata densità di energia della pelle per una fabbricazione di successo. In questo studio, l'acciaio inossidabile 316L è stato utilizzato per la produzione della girante chiusa attraverso la tecnologia LPBF. Per ottenere parti stampate di successo e migliorare la qualità complessiva delle giranti chiuse, è necessario garantire una combinazione ottimale di diversi fattori cruciali.
- L'utilizzo di una girante più piccola e grande con un angolo di costruzione di 30˚ riduce notevolmente i difetti e i danni durante il processo di produzione, mostrando risultati superiori rispetto ai casi in cui l'angolo di costruzione è impostato a 90˚.
- L'allineamento della densità di energia verso il basso con la densità di energia verso l'interno con un angolo di 30° garantisce una stampa della girante senza difetti.
- Quando la densità di energia verso il basso rappresenta solo il 20% della densità di energia verso l'interno, si verificano danni evidenti sul pezzo. Anche nei casi in cui non si osservano danni, sulla superficie della girante chiusa si manifestano segni di bruciatura e difetti, particolarmente evidenti nelle giranti chiuse più grandi.
- L'aumento della densità di energia a 55,55 J/mm3 porta a una riduzione della polvere non fusa durante il processo.
- L'aumento della densità di energia riduce la rugosità superficiale a 12,79 µm quando la densità di energia è di 55 J/mm3.
- La durezza della girante varia tra 226 e 233 HV, raggiungendo il massimo a 233 HV quando la densità di energia è di 41,66 J/mm3.
Riferimenti
[1] P. Sulzer, Principi fisici, Manuale delle pompe centrifughe, 2010, pp. 1-26.
[2] J.J.M. Timothy, C. Allison, Aaron M. Rimpel, Jason C. Wilkes, Robert Pelton, Karl Wygant,
Esperienza di produzione e test con la sinterizzazione laser diretta di metalli per giranti di compressori centrifughi chiusi, 43° Turbomachinery & 30th Pump Users Symposia, Pump & Turbo 2014, Houston, TX, 2014.
[3] A.A. Scot Laney, Derrick Bauer, Evaluation of Various Methods for Manufacturing One Piece, Small Tip Opening Centrifugal Compressor Impellers, Asia Turbomachinery and Pump Symposium, Marina Bay Sands, Singapore, 2016
Sands, Singapore, 2016.
[4] Meli, E.; Rindi, A.; Ridolfi, A.; Furferi, R.; Buonamici, F.; Iurisci, G.; Corbò, S.; Cangioli, F. Design and Production of Innovative Turbomachinery Components via Topology Optimization and Additive Manufacturing
Manufacturing. Int. J. Rotating Mach. 2019, 2019, 1-12, https://doi.org/10.1155/2019/9546831.
[5] Lezama-Nicolás, R.; Rodríguez-Salvador, M.; Río-Belver, R.; Bildosola, I. Un metodo bibliometrico per valutare la maturità tecnologica: il caso della manifattura additiva. Scientometrics 2018, 117, 1425- 1452, https://doi.org/10.1007/s11192-018-2941-1.
[6] Aota, L.S.; Bajaj, P.; Sandim, H.R.Z.; Jägle, E.A. Laser Powder-Bed Fusion as an Alloy Development Tool: Selezione dei parametri per la lega in situ con polveri elementari. Materials 2020, 13, 3922, doi:10.3390/ma13183922.
[7] Keshavarzkermani, A.; Marzbanrad, E.; Esmaeilizadeh, R.; Mahmoodkhani, Y.; Ali, U.; Enrique, P.D.; Zhou, N.Y.; Bonakdar, A.; Toyserkani, E. An investigation into the effect of process parameters on melt pool geometry, cell spacing, and grain refinement during laser powder bed fusion. Opt. Laser
Technol. 2019, 116, 83-91, https://doi.org/10.1016/j.optlastec.2019.03.012.
[8] Qu, S.; Ding, J.; Fu, J.; Fu, M.; Zhang, B.; Song, X. Trattamento di alta precisione della fusione laser a letto di polvere di rame puro. Addit. Manuf. 2021, 48, https://doi.org/10.1016/j.addma.2021.102417.
[9] Huang, S.; Narayan, R.L.; Tan, J.H.K.; Sing, S.L.; Yeong, W.Y. Risolvere il dilemma porosità-inclusione non fusa durante la fusione in situ
inclusione durante la lega in situ di Ti34Nb tramite fusione laser a letto di polvere. Acta Mater. 2020, 204, 116522, https://doi.org/10.1016/j.actamat.2020.116522.
[10] Mukherjee, T., Wei, H.L., De, A. e DebRoy, T., 2018. Heat and fluid flow in additive manufacturing- Part II: Powder bed fusion of stainless steel, and titanium, nickel and aluminium base alloys.
Computational Materials Science, 150, pp.369-380.
[11] Aota, L.S.; Bajaj, P.; Sandim, H.R.Z.; Jägle, E.A. Laser Powder-Bed Fusion as an Alloy Development Tool: Selezione dei parametri per la lega in situ con polveri elementari. Materials 2020, 13, 3922, doi:10.3390/ma13183922.
[12] Fernández, S.; Jiménez, M.; Porras, J.; Romero, L.; Espinosa, M.M.; Domínguez, M. Produzione additiva e prestazioni di pompe idrauliche funzionali
Produzione additiva e prestazioni di giranti di pompe idrauliche funzionali nella tecnologia di modellazione a deposizione fusa. J. Mech. Des. 2015, 138, 024501, https://doi.org/10.1115/1.4032089.
[13] Ponticelli, G.S.; Tagliaferri, F.; Venettacci, S.; Horn, M.; Giannini, O.; Guarino, S. Re-Engineering di una girante per pompa elettrica sommersa da produrre mediante fusione laser selettiva. Appl. Sci. 2021, 11, 7375, https://doi.org/10.3390/app11167375.
[14] Mikula, J.; Ahluwalia, R.; Laskowski, R.; Wang, K.; Vastola, G.; Zhang, Y.-W. Modellazione dell'influenza dei parametri di processo sulla formazione di precipitati nella produzione additiva per fusione a letto di polvere di
IN718. Mater. Des. 2021, 207, 109851, https://doi.org/10.1016/j.matdes.2021.109851.
[15] O'brien, J.; Montgomery, S.; Yaghi, A.; Afazov, S. Simulazione della catena di processo della fusione laser a letto di polvere, compresi il trattamento termico e l'indurimento superficiale. CIRP J. Manuf. Sci. Technol. 2021, 32, 266-276,
https://doi.org/10.1016/j.cirpj.2021.01.006.
[16] Yavari, R.; Williams, R.; Riensche, A.; Hooper, P.A.; Cole, K.D.; Jacquemetton, L.; Halliday, H.(.; Rao, P.K. Thermal modeling in metal additive manufacturing using graph theory - Application to laser powder bed fusion of alarge volume impeller. Addit. Manuf. 2021, 41, 101956,
https://doi.org/10.1016/j.addma.2021.101956.
[17] Tupac-Yupanqui, H.; Armani, A. Additive Manufacturing of Functional Inconel 718 Parts from Recycled Materials. J. Mater. Eng. Perform. 2021, 30, 1177-1187, https://doi.org/10.1007/s11665-020-05402-8.
[18] Kladovasilakis, N.; Kontodina, T.; Charalampous, P.; Kostavelis, I.; Tzetzis, D.; Tzovaras, D. A Case Study on 3D Scanning, Digital Reparation and Rapid Metal Additive Manufacturing of a Centrifugal Impeller. In Proceedings of the 24th Innovative Manufacturing Engineering and Energy International Conference (IManEE), Atene, Grecia, 14-15 dicembre 2020, https://doi.org/10.1088/1757-
899x/1037/1/012018.
[19] Tian, Y.; Ren, H.; He, J.; Zha, X.; Lin, K.; Zhou, M.; Xiong, Y. Miglioramento della rugosità superficiale delle strutture a sbalzo in lega Ti- 6Al-4V tramite l'ottimizzazione del processo di fusione laser a letto di polvere. J. Manuf.
Process. 2024, 110, 434-446, https://doi.org/10.1016/j.jmapro.2024.01.008.
[20] Guo, J.; Wang, Y.; Wang, Y.; Peng, S.; Wang, F. Simulation Study on the Energy Utilization Efficiency of a Turbine Impeller Based on a Selective Laser Melting Process. Appl. Sci. 2023, 13, 10657,
https://doi.org/10.3390/app131910657.
[21] Yaghi, A.; Ayvar-Soberanis, S.; Moturu, S.; Bilkhu, R.; Afazov, S. Design against distortion for additive manufacturing. Addit. Manuf. 2019, 27, 224-235, https://doi.org/10.1016/j.addma.2019.03.010.
[22] Kumar, A.; Shandiz, M.A.; Sikan, F.; Brochu, M. Proprietà microstrutturali e meccaniche di una girante chiusa IN625 priva di supporto interno prodotta mediante fusione laser a letto di polvere (L-PBF). Mater. Sci. Eng.
A 2023, 874, https://doi.org/10.1016/j.msea.2023.145080.
[23] O.D. Ian Campbell, Kowen Joseph, Wohlers Terry, 3D Prinitng and Additive Manufacturing Global State of the Industry, Wholers Report, Wholers Associates, 2018.
[24] Herzog, D.; Asami, K.; Scholl, C.; Ohle, C.; Emmelmann, C.; Sharma, A.; Markovic, N.; Harris, A. Linee guida di progettazione per la fusione laser a letto di polvere in Inconel 718.J. Laser Appl. 2022, 34, 012015,
https://doi.org/10.2351/7.0000508.
[25] Rebaioli, L.; Fassi, I. Una rassegna sugli artefatti di riferimento per la valutazione delle prestazioni geometriche dei processi di produzione additiva. Int. J. Adv. Manuf. Technol. 2017, 93, 2571-2598,
https://doi.org/10.1007/s00170-017-0570-0.
[26] Yang, S.; Tang, Y.; Zhao, Y.F. Un nuovo metodo di consolidamento delle parti per sfruttare la libertà di progettazione della produzione additiva
produzione additiva. J. Manuf. Process. 2015, 20, 444-449, https://doi.org/10.1016/j.jmapro.2015.06.024.
[27] Grasso, M.; Laguzza, V.; Semeraro, Q.; Colosimo, B.M. Monitoraggio in-process della fusione laser selettiva
Selective Laser Melting: Rilevamento spaziale dei difetti attraverso l'analisi dei dati di immagine. J. Manuf. Sci. Eng. 2016, 139, 051001, https://doi.org/10.1115/1.4034715.
[28] Li, J.; Cao, L.; Xu, J.; Wang, S.; Zhou, Q. Classificazione intelligente della porosità in situ nella fusione laser selettiva basata sul monitoraggio coassiale e sull'elaborazione delle immagini. Misura 2021, 187, 110232,
https://doi.org/10.1016/j.measurement.2021.110232.
[29] Leung, C.L.A.; Marussi, S.; Atwood, R.C.; Towrie, M.; Withers, P.J.; Lee, P.D. Imaging a raggi X in situ della dinamica dei difetti e delle piscine fuse nella fusione laser selettiva
dinamiche dei difetti e della piscina fusa nella produzione additiva laser. Nat. Commun. 2018, 9, 1-9, https://doi.org/10.1038/s41467-018-03734-7.
[30] Cacace, S.; Pagani, L.; Colosimo, B.M.; Semeraro, Q. L'effetto della densità di energia e della struttura della porosità sulle proprietà di trazione dell'acciaio inossidabile 316L
sulle proprietà di trazione dell'acciaio inossidabile 316L prodotto mediante fusione laser a letto di polvere. Prog. Addit. Manuf. 2022, 7, 1053-1070, https://doi.org/10.1007/s40964-022-00281-y.
[31] Sun, Z.J.; Tan, X.P.; Tor, S.B.; Yeong, W.Y. Fusione laser selettiva di acciaio inossidabile 316L a bassa porosità e alta velocità di costruzione
porosità e alti tassi di accumulo. Mater. Des. 2016, 104, 197-204, https://doi.org/10.1016/j.matdes.2016.05.035.
[32] Clijsters S, Craeghs T, Buls S, Kempen K, Kruth JP (2014) Controllo di qualità in situ del processo di fusione laser selettiva mediante un sistema di monitoraggio del pool di fusione ad alta velocità e in tempo reale. Int J Adv Manuf Technol. https:// doi. org/ 10. 1007/ s00170-014-6214-8
[33] Lippolis, V., Irurhe, O., Porricelli, A. C. R., Cortese, M., Schena, R., Imafidon, T., et al. (2017). Co-occorrenza naturale di aflatossine e ocratossina A nello zenzero (Zingiber officinale) della Nigeria. Food control 73, 1061-1067. https://doi.org/10.1016/j. foodcont.2016.10.026
[34] Gu, D.; Shen, Y. Fenomeni di balling nella sinterizzazione laser diretta di polvere di acciaio inossidabile: Meccanismi metallurgici e metodi di controllo. Mater. Des. 2009, 30, 2903-2910,
https://doi.org/10.1016/j.matdes.2009.01.013.
[35] Eliasu, A.; Czekanski, A.; Boakye-Yiadom, S. Effetto dei parametri di fusione a letto di polvere laser sull'evoluzione microstrutturale e la durezza dell'acciaio inossidabile 316L
evoluzione microstrutturale e sulla durezza dell'acciaio inossidabile 316L. Int. J. Adv. Manuf. Technol. 2021, 113, 2651-2669, https://doi.org/10.1007/s00170-021-06818-9.