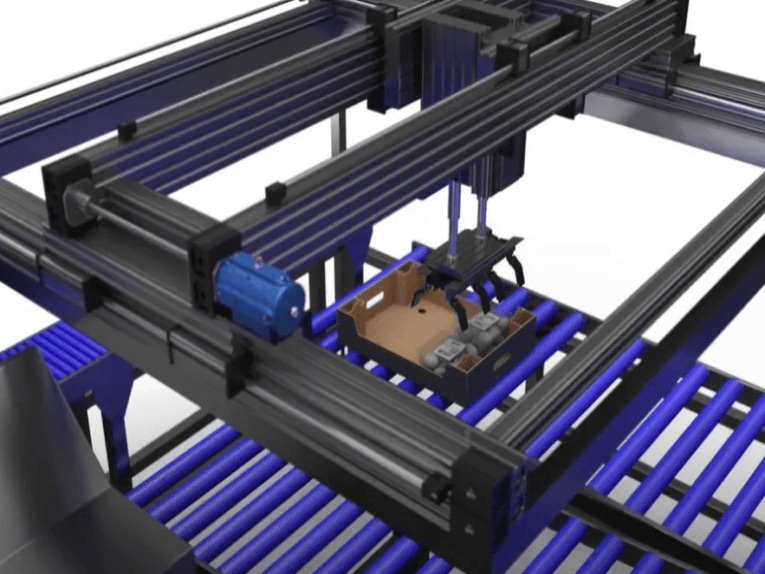
Vedi traduzione automatica
Questa è una traduzione automatica. Per vedere il testo originale in inglese cliccare qui
#News
Utilizzo di motori ad albero lineare in parallelo
Forza elevata e funzionamento solido.
La maggior parte delle persone pensa ai sistemi di azionamento parallelo come a quelli presenti nei robot cartesiani/gantry. Ma i sistemi di azionamento parallelo possono anche essere considerati come due o più motori lineari che lavorano in parallelo da un unico controllore di azionamento. Questo copre i robot di tipo cartesiano/gantry e altre aree importanti del controllo del movimento, come i robot ad alta e altissima precisione a singolo asse con risoluzione e precisione di posizione nell'intervallo tra i subnanometri e gli alti picometri. Questi sistemi trovano applicazione in settori quali l'ottica e i microscopi, la produzione di semiconduttori, le macchine utensili, gli attuatori con forza elevata, le apparecchiature per il collaudo dei materiali, il pick-and-place, le operazioni di assemblaggio, la manipolazione di macchine utensili e la saldatura ad arco. In definitiva, esistono applicazioni sia nel mondo del micron che in quello del submicron.
Problemi con i motori paralleli
Il problema principale di tutti i sistemi ad azionamento parallelo è l'allineamento ortogonale: la capacità di mantenere l'asse parallelo in quadratura. Nei sistemi ad azionamento meccanico come viti, cremagliere, cinghie e catene, il problema principale è il vincolo del sistema meccanico dovuto al disallineamento o alle tolleranze sovrapposte. Nei sistemi ad azionamento diretto, si aggiunge il problema dell'errore sinusoidale introdotto a causa degli errori di installazione e delle variazioni dei motori lineari.
La pratica più comune per superare questi problemi consiste nell'azionare e controllare ciascun lato del sistema parallelo in modo indipendente, ma sincronizzandoli elettronicamente. Il costo di questo sistema è elevato perché richiede il doppio dell'elettronica di azionamento e di rilevamento della posizione rispetto a un sistema a un asse. Inoltre, aggiunge errori di sincronizzazione e di inseguimento che possono degradare le prestazioni del sistema.
L'elemento che rende possibile il collegamento in parallelo dei motori ad albero lineare è un motore altamente reattivo. Il movimento dinamico generato da due motori ad albero lineare identici è lo stesso quando si riceve lo stesso segnale di controllo.
Come in tutti i sistemi di azionamento in parallelo, i motori ad albero lineare devono essere accoppiati fisicamente con un meccanismo che consenta all'asse un movimento a un solo grado di libertà. In questo modo, i motori ad albero lineare in parallelo agiscono come un'unica unità per consentire il funzionamento con un unico encoder e un unico servocomando. Inoltre, poiché un motore ad albero lineare correttamente installato funziona senza contatto, non può introdurre alcun vincolo meccanico nel sistema.
Queste affermazioni sono valide per qualsiasi motore lineare senza contatto. I motori ad albero lineare si differenziano dagli altri motori lineari senza contatto per diversi aspetti che ne consentono l'utilizzo in applicazioni parallele.
Il design del motore ad albero lineare pone il magnete permanente al centro del campo elettromagnetico, rendendo il traferro non critico. La bobina circonda completamente il magnete, quindi l'effetto netto del campo magnetico è la forza. Ciò elimina virtualmente qualsiasi variazione di forza causata da una differenza nel traferro, dovuta a disallineamento o a differenze di lavorazione, rendendo semplice l'allineamento e l'installazione del motore.
Tuttavia, l'errore sinusoidale - un problema importante - può causare differenze di forza in qualsiasi motore lineare senza contatto.
I motori lineari, come i motori ad albero lineare, sono definiti motori sincroni. In effetti, la corrente viene applicata alla bobina per formare un elettromagnete che si sincronizza con il campo magnetico dei magneti permanenti nella pista magnetica. La forza in un motore lineare è generata dall'intensità relativa di questi campi magnetici e dall'angolo del loro disallineamento intenzionale.
In un sistema di azionamento parallelo, tutte le bobine e le tracce magnetiche diventano un unico motore quando tutti i loro campi magnetici sono perfettamente allineati. Tuttavia, qualsiasi disallineamento delle bobine o delle tracce magnetiche causerà un disallineamento dei campi magnetici, producendo forze diverse in ciascun motore. Questa differenza di forza può, a sua volta, vincolare il sistema. L'errore sinusoidale è quindi la differenza di forze prodotta dal disallineamento delle bobine o delle piste magnetiche.
L'errore sinusoidale può essere calcolato con la seguente equazione:
Fdif = Fgen × sin(2πDdif/MPn-n)
dove Fdif = differenza di forza tra le due bobine, Fgen = forza generata, Ddif = lunghezza del disallineamento e MPn-n = passo magnetico nord-nord.
La maggior parte dei motori lineari presenti sul mercato è progettata con un passo magnetico da nord a nord compreso tra 25 e 60 mm, con l'intento di ridurre le perdite IR e la costante di tempo elettrica. Ad esempio, un disallineamento di appena 1 mm in un motore lineare con passo n-n di 30 mm produce una perdita di potenza di circa il 21%.
Il motore ad albero lineare compensa questa perdita utilizzando un passo magnetico nord-nord molto più lungo che riduce l'effetto dell'errore sinusoidale causato da un disallineamento accidentale. Lo stesso disallineamento di 1 mm in un motore ad albero lineare con passo n-n di 90 mm produrrà solo una perdita di potenza del 7%.
Sistemi ad azionamento parallelo
Un posizionamento veramente accurato è possibile per i robot ad asse singolo ad alta e altissima precisione solo quando il feedback si trova direttamente nel centro di massa del punto di lavoro. Anche la forza generata dal motore dovrebbe essere concentrata al centro della massa del punto di lavoro. Tuttavia, in genere è impossibile che il motore e il feedback si trovino esattamente nella stessa posizione!
Se si colloca un encoder al centro della massa e si utilizzano motori paralleli ad albero lineare equidistanti dal centro della massa, si ottiene il feedback e la generazione di forza desiderati al centro della massa. Questo non è possibile per altri tipi di sistemi di azionamento parallelo, che richiedono due serie di encoder e servocomandi per creare questo tipo di azionamento parallelo.
L'azionamento singolo/encoder singolo funziona meglio negli impieghi ad altissima precisione e offre ai costruttori di sistemi a portale un enorme vantaggio. In passato, i sistemi potevano avere due motori diversi che azionavano viti a ricircolo di sfere separate utilizzando due diversi controllori collegati elettronicamente, o addirittura due motori lineari con due encoder collegati elettronicamente con due azionamenti. Ora le stesse azioni possono essere ottenute da due motori ad albero lineare, un encoder e un amplificatore/azionamento, purché la rigidità del sistema sia sufficientemente elevata.
Questo è un vantaggio anche per le applicazioni che richiedono una forza estremamente elevata. È possibile collegare in parallelo un numero qualsiasi di motori ad albero lineare, sommando le loro forze.