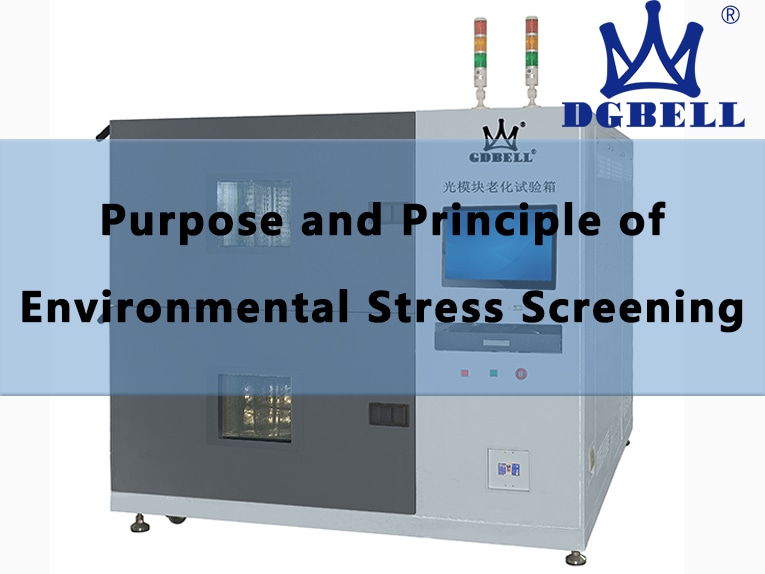
Vedi traduzione automatica
Questa è una traduzione automatica. Per vedere il testo originale in inglese cliccare qui
#News
Scopo e principio dello screening dello stress ambientale
Scopo e principio dello screening dello stress ambientale
Scopo dello screening dello stress ambientale
Lo scopo dello screening delle sollecitazioni ambientali è quello di trovare ed eliminare i guasti precoci dei prodotti, farli entrare nella fase di guasto casuale quando escono dalla fabbrica e consegnarli agli utenti con un livello di affidabilità intrinseco.
Principio dello screening dello stress ambientale
Lo screening dello stress ambientale consiste nell'accelerare la trasformazione dei potenziali difetti interni in guasti applicando uno stress ambientale ed elettrico ragionevole alle apparecchiature elettroniche, in modo da poterli individuare ed eliminare.
Lo screening dello stress ambientale è un mezzo tecnologico per lo sviluppo e la produzione di apparecchiature. L'effetto di screening dipende dallo stress ambientale applicato, dal livello di stress elettrico e dalla capacità degli strumenti di rilevamento. L'entità dello stress applicato determina se i potenziali difetti possono essere accelerati in guasti entro un tempo predeterminato; la capacità di rilevamento determina se i potenziali difetti che sono stati accelerati in guasti dallo stress possono essere individuati per la risoluzione dei problemi. Pertanto, lo screening delle sollecitazioni ambientali può essere considerato come un'estensione del processo di ispezione e collaudo del controllo di qualità del prodotto. 2 classificazione dei difetti
Definizioni generali
La perdita della funzione specificata del prodotto è chiamata guasto. I prodotti riparabili sono spesso definiti guasti. Per le apparecchiature, qualsiasi caratteristica qualitativa non conforme agli standard tecnici specificati costituisce un difetto.
Il guasto della maggior parte delle apparecchiature elettroniche viene definito guasto. Si veda la Figura 2.11 per la sua scomposizione in base alla causa del guasto. Dalla figura si evince che i guasti delle apparecchiature si dividono in guasti accidentali e guasti da difetto. Si ritiene che il guasto accidentale sia un guasto casuale, causato dal tasso di guasto intrinseco dei componenti e delle parti; mentre il guasto di tipo difettoso è causato da difetti delle materie prime, difetti dei componenti, difetti del processo di assemblaggio e difetti di progettazione; i difetti dei componenti stessi sono causati da difetti quali la struttura, il processo e i materiali, mentre i difetti di progettazione includono difetti di progettazione dei circuiti, difetti di progettazione strutturale difetti di progettazione del processo, ecc.
Classificazione dei difetti visivi delle apparecchiature elettroniche
Dal punto di vista dell'impatto e delle conseguenze, i difetti si dividono in difetti fatali, difetti pesanti e difetti leggeri: dal punto di vista visivo, i principali tipi di processo di difetti includono: saldatura, connessione non saldata, eccesso di fili e cavi, gap anti-cortocircuito, contatto, circuito stampato, produzione e installazione di parti, componenti, avvolgimento, marcatura, ecc.
I difetti fatali si riferiscono ai difetti che possono causare danni o insicurezza al personale, come l'uso, la manutenzione, il trasporto e lo stoccaggio delle apparecchiature, o che possono ostacolare le prestazioni tattiche di alcune apparecchiature importanti (come navi, carri armati, grandi artiglierie, aerei, missili, ecc.)
Per difetto maggiore si intende il difetto che può causare un guasto o ridurre seriamente le prestazioni di servizio dell'apparecchiatura, ma non costituisce un difetto fatale.
I difetti leggeri si riferiscono a difetti che non costituiscono difetti gravi, ma che riducono le prestazioni di servizio dell'apparecchiatura o non soddisfano gli standard tecnici specificati e hanno un impatto minimo sull'uso o sul funzionamento dell'apparecchiatura.
Per difetto visivo si intende il difetto che può essere osservato direttamente attraverso gli organi visivi umani o giudicato con semplici strumenti sulle caratteristiche qualitative dell'apparecchiatura.
L'ispettore di qualità dell'unità produttiva può individuare la maggior parte dei difetti visibili e sottoporli ai reparti competenti per la loro eliminazione. Solo i difetti invisibili possono essere individuati attraverso lo screening delle sollecitazioni ambientali o altri metodi, altrimenti l'affidabilità del prodotto ne risentirà.
Principio di progettazione dello schema di screening delle sollecitazioni ambientali
Il principio di progettazione dello schema di test di screening delle sollecitazioni ambientali è quello di consentire alle sollecitazioni di screening di stimolare i difetti causati da potenziali difetti di progettazione, difetti di fabbricazione e difetti dei componenti: le sollecitazioni applicate non devono necessariamente simulare il profilo di vita, il profilo di attività e il profilo ambientale specificati dal prodotto; nel test, devono essere simulate varie modalità di funzionamento specificate dal progetto.
Determinare lo screening di routine o lo screening quantitativo in base alle condizioni e alle necessità: formulare metodi di screening in base alle diverse fasi e alle caratteristiche del prodotto.
Screening in fase di sviluppo
Nella fase di sviluppo, lo screening convenzionale viene generalmente effettuato in base ai metodi di screening ottenuti con l'esperienza. Le sue funzioni principali sono: da un lato, serve a raccogliere informazioni come il tipo e la quantità di possibili difetti nei prodotti e l'effetto dei metodi di screening; dall'altro, i test di routine vengono eseguiti prima dei test di crescita dell'affidabilità e di sviluppo ingegneristico, consentendo di risparmiare tempo e denaro per i test. Allo stesso tempo, favorisce la progettazione di metodi di test maturi e di rapido sviluppo.
Lo screening di routine nella fase di sviluppo deve raccogliere i dati per lo screening quantitativo nella fase di produzione, preparare lo screening quantitativo e progettare lo schema dello screening quantitativo.
Screening nella fase di produzione
Lo screening nella fase di produzione consiste principalmente nell'implementare lo schema di screening quantitativo progettato nella fase di sviluppo; confrontando la precipitazione dei difetti registrati con il valore stimato dal progetto, vengono proposte misure per regolare lo screening e il processo di produzione; migliorare o riformulare lo schema di screening quantitativo facendo riferimento ai dati empirici di screening quantitativo di prodotti con struttura e maturità simili. Questi dati empirici includono principalmente:
Modelli di componenti e componenti ad alto tasso di guasto: fornitori di prodotti ad alto tasso di guasto; dati di ispezione, test e screening dei componenti: registrazioni di screening e test precedenti; registrazioni di test di crescita dell'affidabilità: altre registrazioni di test.
Effetto dello stress ambientale sui difetti
Le sollecitazioni ambientali in campo sono il fattore principale che influisce sullo sviluppo dei difetti in guasti. Ogni difetto che si trasforma in difetto deve essere sottoposto a un certo stress di resistenza. Dopo un certo periodo di tempo, solo quando il prodotto è sottoposto a uno stress ambientale pari o superiore alla soglia, alcuni difetti possono diventare difetti: in presenza di stress ambientali lievi, molti difetti non si trasformano in difetti. Pertanto, lo scopo dello screening può essere raggiunto solo selezionando come condizione di screening la sollecitazione che può esporre alcuni difetti.
Conclusione
Lo screening dello stress ambientale è il processo tecnologico di sviluppo e produzione dell'intera macchina. Ogni prodotto deve essere realizzato. Per risparmiare risorse e tempo, dobbiamo cercare di selezionare le condizioni di stress ad alta efficienza e il grado di assemblaggio a basso costo. Le apparecchiature per le vibrazioni casuali e i cicli di temperatura sono necessari e il produttore dovrebbe attrezzarsi il prima possibile. Prima di essere attrezzato, può essere implementato in unità vicine con queste condizioni. A questo punto, è più importante selezionare e vagliare il livello di assemblaggio.
La progettazione dello schema di screening dello stress ambientale è un lavoro completo. È necessario conoscere la storia e la situazione attuale del progetto del prodotto, del processo e dei componenti e raccogliere i dati necessari: quando si seleziona lo screening dello stress ambientale o lo screening quantitativo dello stress ambientale e quale livello di assemblaggio selezionare, si devono dedurre alcuni rischi. Pertanto, è necessario applicare il metodo dell'ingegneria di sistema per effettuare un trade-off completo intorno ai requisiti di affidabilità del prodotto.
Lo screening delle sollecitazioni ambientali e il test di crescita dell'affidabilità fanno parte dei test di ingegneria dell'affidabilità. Hanno gli stessi obiettivi generali e le proprie caratteristiche. Possono completarsi a vicenda, ma non sostituirsi. Lo screening dello stress ambientale può essere utilizzato per effettuare alcuni test di crescita dell'affidabilità, in modo da sfruttare appieno i risultati dello screening dello stress ambientale e migliorare l'efficienza del test.