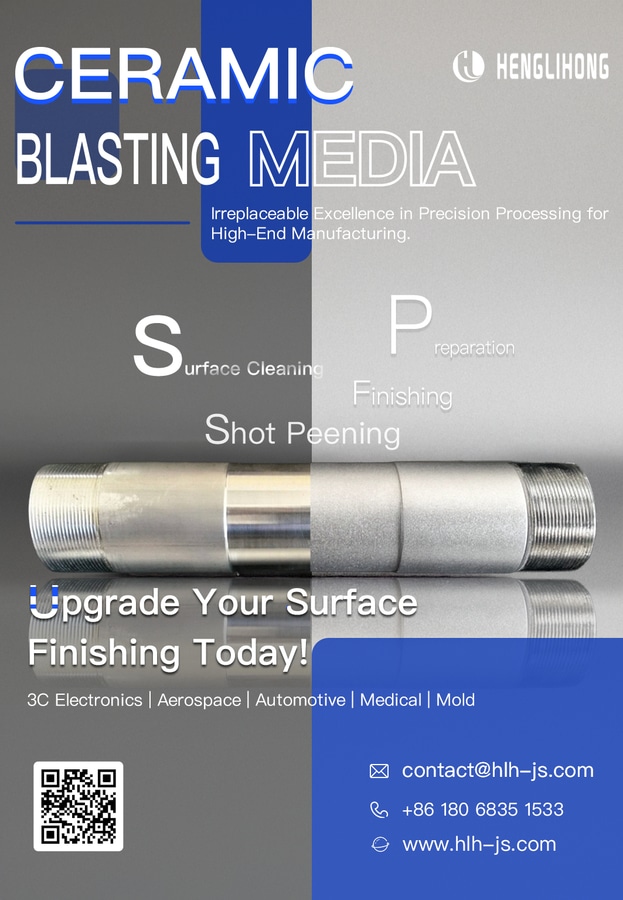
Vedi traduzione automatica
Questa è una traduzione automatica. Per vedere il testo originale in inglese cliccare qui
#News
Applicazioni industriali e prospettive della tecnologia di granigliatura ceramica a livello micrometrico
Esplorare il futuro del trattamento di precisione delle superfici nella produzione con la tecnologia di granigliatura ceramica a livello di micron
Nel campo della moderna produzione di precisione, la tecnologia di trattamento delle superfici svolge un ruolo cruciale. Con l'aumento delle richieste di qualità delle superfici in settori ad alta tecnologia come l'elettronica, l'aerospaziale e i dispositivi medici, le tecnologie di granigliatura tradizionali non sono più in grado di soddisfare i requisiti di lavorazione a livello di micron. La tecnologia di granigliatura ceramica a livello micron, come metodo emergente di trattamento superficiale ad alta precisione, sta gradualmente diventando un processo indispensabile nella produzione di pezzi di precisione. Questo articolo analizzerà a fondo i principi, le applicazioni e le tendenze di sviluppo di questa tecnologia.
1. Principi tecnici
1.1 Caratteristiche del materiale delle microsfere di ceramica
Le perle ceramiche di livello micron sono realizzate principalmente con materiali ceramici ad alta durezza come l'ossido di zirconio (ZrO₂), l'ossido di alluminio (Al₂O₃) o il carburo di silicio (SiC), con diametri che variano in genere da 5 a 100 micron. Questi materiali possiedono le seguenti caratteristiche:
Durezza elevatissima: Durezza Mohs di 8-9,5, che si avvicina a quella del diamante
Eccellente sfericità: Sfericità superiore al 98%, che garantisce superfici di contatto uniformi
Stabilità chimica: Resistente agli acidi e agli alcali, non reattivo con la maggior parte dei metalli
Precisione dimensionale: Distribuzione uniforme delle dimensioni delle particelle con deviazione standard controllata entro ±1μm
1.2 Meccanismo di lavoro
La tecnologia di granigliatura con microsfere ceramiche utilizza un flusso d'aria o di liquido ad alta pressione come vettore per proiettare microsfere ceramiche sulla superficie del pezzo a velocità (20-120 m/s) e angoli (15°-90°) controllati con precisione. I microscopici effetti di impatto prodotti dalla collisione delle perle di ceramica con la superficie consentono di modificarla con precisione:
Microtaglio: I bordi delle perle ceramiche eseguono microtagli sulla superficie, rimuovendo strati superficiali di livello nanometrico
Deformazione plastica: Le forze d'impatto creano microscopiche deformazioni plastiche sulla superficie del materiale, aumentando la durezza superficiale
Stress nano-compressivo: Forma un campo di stress compressivo nello strato superficiale, migliorando la resistenza alla fatica
Attivazione superficiale: Aumenta i siti attivi della superficie, migliorando l'adesione del rivestimento successivo
2. Apparecchiature e parametri di processo
2.1 Componenti principali dell'apparecchiatura
I moderni sistemi di granigliatura ceramica a livello di micron includono in genere i seguenti componenti:
Sistema di controllo della pressione ad alta precisione: Fluttuazione della pressione controllata entro ±0,01MPa
Dispositivo di classificazione della polvere a livello di micron: Assicura la coerenza delle dimensioni delle particelle
Sistema di controllo digitale dell'ugello: Controlla con precisione l'angolo di proiezione e la distanza
Sistema di monitoraggio ottico in tempo reale: Monitora gli effetti della lavorazione e regola i parametri in tempo reale
Unità di controllo ambientale: Temperatura controllata a 20±2℃, umidità al 45±5%
2.2 Parametri chiave del processo e controllo
Parametro, intervallo di controllo, fattori di influenza
Pressione di sabbiatura: 0,1-0,8MPa, Rugosità superficiale, efficienza di lavorazione
Diametro del cordone: 5-100μm, morfologia superficiale, microstruttura
Angolo di proiezione: 15°-90°, direzione della forza d'urto, tasso di rimozione del materiale
Distanza di proiezione: 10-100 mm, distribuzione dell'energia, uniformità del trattamento
Tempo di lavorazione: 5-300s, integrità della superficie, profondità di lavorazione
Densità di flusso delle microsfere: 2-20g/min-cm², efficienza di lavorazione, qualità della superficie
Il controllo preciso di questi parametri è fondamentale per ottenere effetti superficiali ideali. I sistemi moderni utilizzano in genere algoritmi di intelligenza artificiale per assistere l'ottimizzazione dei parametri, generando automaticamente combinazioni di parametri ottimali in base alle caratteristiche del materiale e ai requisiti di lavorazione.
3. Campi di applicazione
3.1 Industria dei semiconduttori e della microelettronica
Lavorazione di precisione del lead frame: Aumenta la resistenza dell'incollaggio del 30-50%
Pulizia dei sistemi microelettromeccanici (MEMS): Rimuove i contaminanti microscopici, migliorando la resa fino al 15%
Trattamento del substrato di confezionamento dei circuiti integrati: Migliora la bagnabilità della superficie, migliorando l'affidabilità della saldatura
3.2 Campo aerospaziale
Rafforzamento delle pale delle turbine a gas: Aumenta la vita a fatica delle pale fino al 40%
Trattamento di precisione dei componenti idraulici: Riduce il coefficiente di attrito, prolungando la durata di servizio
Trattamento superficiale dei dispositivi di fissaggio aerospaziali: Migliora la resistenza all'infragilimento da idrogeno e la resistenza alla corrosione
3.3 Dispositivi medici
Modifica della superficie degli impianti: Migliora l'osteointegrazione e la biocompatibilità
Trattamento degli impianti dentali: Crea microstrutture che favoriscono la crescita dei tessuti
Componenti di dispositivi medici di precisione: Rimuove le microbave, migliorando la sicurezza
4. Vantaggi tecnici e limiti
4.1 Vantaggi rispetto alle tecnologie di sabbiatura tradizionali
Maggiore precisione di lavorazione: Può ottenere una modifica della superficie a livello nanometrico, con valori di Ra controllabili entro 0,05-1,2μm
Integrità della superficie: Non produce praticamente microfratture o concentrazioni di stress
Ripetibilità: Consistenza da lotto a lotto superiore al 95%
Rispetto dell'ambiente: I materiali ceramici possono essere riciclati, riducendo la produzione di rifiuti
Controllo preciso dell'area: Possibilità di ottenere un trattamento selettivo dell'area a livello di micron
4.2 Limitazioni e sfide tecniche
Costo di investimento delle apparecchiature: Le attrezzature professionali richiedono in genere un investimento di 500.000-2.000.000 di yuan
Finestra di processo ristretta: Elevati requisiti di controllo dei parametri, operazioni difficili
Problemi di adattabilità a materiali specifici: Come ad esempio i materiali ultramorbidi o alcuni compositi
Efficienza di produzione: Minore superficie trattata per unità di tempo rispetto ai metodi tradizionali
5. Tendenze di sviluppo della tecnologia più recente
5.1 Intelligenza e gemelli digitali
Ottimizzazione dei parametri assistita dall'intelligenza artificiale: Riduce i tempi di prova e di errore fino all'85%
Tecnologia Digital Twin: Simulazione in tempo reale del processo di sabbiatura, con previsione della qualità della superficie
Sistemi di controllo adattivi: Regolazione automatica dei parametri di processo in base al feedback in tempo reale
5.2 Nuovi materiali ceramici
Microsfere di ceramica strutturate a guscio: Combinazione di elevata durezza e tenacità
Ceramica nano-composita: miglioramento della resistenza all'usura e della stabilità chimica
Perle di ceramica funzionalizzate: Modifica della superficie con gruppi funzionali specifici, per ottenere un'attivazione chimica
5.3 Integrazione del processo composito
Micropallinatura elettrochimica assistita: Combinazione di effetti elettrochimici per migliorare l'efficienza di rimozione del materiale
Sabbiatura ceramica potenziata con il laser: Utilizzo del pretrattamento laser per migliorare la precisione di lavorazione
Tecnologia assistita da ultrasuoni: Migliora gli effetti di impatto delle microsfere riducendo la pressione di proiezione
6. Caso di studio: Trattamento della lama di Aero-Engine
Un produttore di motori aeronautici ha adottato sfere ceramiche di livello micron (ZrO₂, 20±2μm) per trattare le pale delle turbine in lega ad alta temperatura, ottenendo i seguenti risultati significativi:
Rugosità superficiale ottimizzata da Ra 1,8μm a Ra 0,4μm
Durezza superficiale aumentata del 42%, da HV320 a HV455
La profondità dello strato di stress compressivo superficiale ha raggiunto i 25μm, migliorando la vita a fatica del 35%
L'adesione del rivestimento a barriera termica è migliorata del 50%, con un prolungamento della vita utile di 2.000 ore
L'efficienza produttiva è aumentata del 20%, con una riduzione del 75% del tasso di rilavorazione della lavorazione
Questo caso convalida pienamente le prestazioni superiori della tecnologia di granigliatura ceramica a livello di micron nel trattamento superficiale di componenti di precisione di fascia alta.
7. Guida all'implementazione del processo e controllo qualità
7.1 Flusso di lavoro per l'implementazione del processo< strong>
Pretrattamento: Lavaggio a ultrasuoni per rimuovere olio e particolato
Progettazione dei parametri: Impostazione dei parametri iniziali in base alle caratteristiche e ai requisiti del materiale
Convalida del campione: Test su piccoli lotti e analisi della superficie
Elaborazione formale: Controllo delle condizioni ambientali, esecuzione delle operazioni di sabbiatura
Ispezione della qualità: Rugosità della superficie, morfologia e test delle prestazioni
Post-trattamento: Neutralizzazione della superficie, rimozione delle particelle ceramiche residue
7.2 Controllo di qualità e metodi di prova
Elemento di prova, attrezzatura di prova, standard di controllo
Rugosità superficiale: Laser Confocale / Microscopio, Ra ±0,05μm
Morfologia superficiale: SEM a emissione di campo, assenza di microfratture, distribuzione uniforme delle particelle
Strato di tensione di compressione: Analizzatore di stress a raggi X, valore di stress -300±30MPa
Durezza superficiale: Tester di nano-indentazione, deviazione della durezza <5%
Attività superficiale: Misuratore dell'angolo di contatto, riduzione dell'angolo di contatto >40%
Conclusione
Come processo all'avanguardia per il trattamento superficiale di parti di precisione, la tecnologia di granigliatura ceramica a livello di micron continua a superare i limiti della lavorazione tradizionale, fornendo un potente supporto tecnico alle industrie manifatturiere ad alta tecnologia. Le sue applicazioni nel settore aerospaziale, nei dispositivi medici, nei semiconduttori e in altri campi hanno fortemente promosso il progresso tecnologico di queste industrie. Con lo sviluppo della produzione intelligente e delle nuove tecnologie dei materiali, la tecnologia di granigliatura ceramica a livello di micron integrerà ulteriormente concetti avanzati come l'intelligenza artificiale e i gemelli digitali per ottenere una maggiore precisione e un trattamento superficiale più efficiente, offrendo nuove opportunità di sviluppo per la produzione di precisione.
Quando introducono questa tecnologia, le imprese devono considerare in modo esaustivo i costi di investimento, i requisiti tecnici e gli scenari applicativi per formulare strategie di implementazione ragionevoli e sfruttare appieno il suo potenziale nel miglioramento della qualità dei prodotti e nell'ottimizzazione dei costi.
Parole chiave: #Sfere di ceramica al micron #Tecnologia di sabbiatura #Trattamento della superficie #Produzione di precisione #Aerospazio #Dispositivi medici