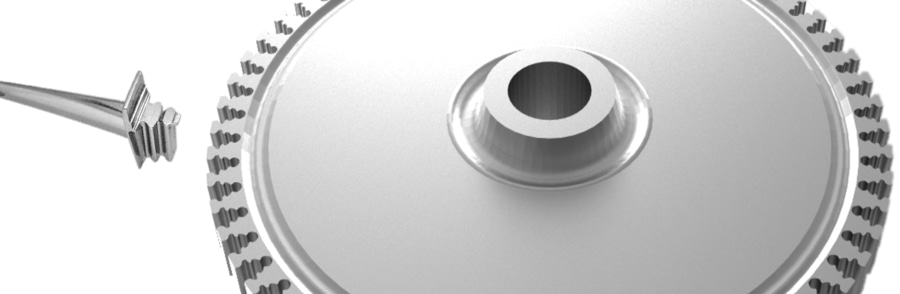
#Tendenze
PROCESSO AFFIDABILE E RIPRODUCIBILE: ARROTONDAMENTO DI SCANALATURE DI ABETE
SBAVATURA E ARROTONDAMENTO DEI DISCHI DI TURBINE
SCANALATURA DI ABETE E PIEDINI DELLA PALA DI TURBINA: LA FEDELTÀ ALLA FORMA È LA MASSIMA PRIORITÀ
I dischi della turbina e del compressore sono dotati di scanalature di supporto, le cosiddette scanalature di abete, in cui so-no inserite le pale della turbina. La brocciatura, l'elettroerosione a filo o la fresatura si sono affermati come metodo di produ-zione per queste scanalature di supporto. Questo crea sbavature o spigoli vivi nella scanalatura di abete. Per un corretto montaggio e per evitare danni, i bordi della scanalatura di abete e quelli del piedino della pala devono essere privi di sbavatu-re e dotati di un raggio definito. Questo è l'unico modo per garantire il corretto funzionamento dei componenti. In particolare, le superfici di pressione dove il piedino della pala e il disco vengono a contatto durante il funzionamento sono soggette a tol-leranze molto basse di 10-20 µm. Nel processo di sbavatura e arrotondamento, non devono esserci deviazioni di forma sulle superfici di pressione in modo che le pale siano perfettamente in posizione.
RIPETIBILITÀ - PERCHÉ LE PROCEDURE ROBOTIZZATE NON SONO LA SCELTA MIGLIORE
Lo stato dell'arte per questa fase del processo è la sbavatura e l'arrotondamento meccanico, in parte controllati da robot, con mole abrasive o spazzole. Le mole utilizzate si usurano nel tempo, il che significa che i risultati della lavorazione non ri-mangono costanti per tutta la durata utile dell'utensile. Gli spigoli vivi tagliano le punte delle spazzole, ad esempio, e causa-no un'usura della spazzola difficile da calcolare, con risultati variabili e un'alta contaminazione del processo causata dai re-sidui della spazzola. Anche gli abrasivi sono soggetti a un'usura irregolare, che deve essere compensata meccanicamente tramite robot. L'abrasione provoca l'ingresso di impurità nel processo.
In caso di geometrie complesse del pezzo, l'arrotondamento è spesso asimmetrico, poiché l'utensile abrasivo o la spazzola possono adattarsi solo in misura limitata alla geometria della scanalatura di abete o non è possibile raggiungere affatto i punti più stretti. Ciò si traduce in arrotondamenti asimmetrici e, di conseguenza, variabili, che spesso comportano il manca-to rispetto delle tolleranze, deviazioni di forma e quindi un aumento degli scarti e dei costi.
CONFRONTO TRA PROCESSI ALTERNATIVI
Alla ricerca di un processo alternativo con risultati di lavorazione più convincenti, un produttore di motori ha valutato due di-verse tecnologie di vibrofinitura insieme a OTEC:
Il primo metodo nella vasca vibrante si è rivelato inefficace per questa applicazione, poiché le smussature non potevano essere portate completamente nell'intervallo di tolleranza anche dopo diverse ore di processo. L'arrotondamento ottenuto non è risultato né simmetrico né ripetibile nelle prove effettuate. Inoltre, l'aumento del livello di rumore e le relative vibrazioni si sono rivelati problematici, poiché nelle immediate vicinanze vengono utilizzati strumenti di misurazione sensibili.
Il secondo, nella macchina di finitura a flusso abrasivo o Streamfinish OTEC, ha già ottenuto risultati promettenti al primo tentativo in brevissimo tempo. Grazie al posizionamento mirato del componente nel processo, tutte le smussature rientrava-no nella tolleranza entro 15 minuti dal tempo di inizio e mostravano un arrotondamento molto simmetrico su tutto il bordo. Ul-teriori test hanno inoltre dimostrato la riproducibilità e la stabilità del processo. La deviazione della forma sulle superfici di pressione poteva essere mantenuta così bassa a meno di 1 µm in modo che non fossero necessarie regolazioni al proces-so di brocciatura a monte. Il processo a bassa vibrazione e bassa rumorosità può essere utilizzato anche in prossimità di di-spositivi di misurazione sensibili.
QUESTI VANTAGGI HANNO GIÀ CONVINTO DIVERSI PRODUTTORI DI MOTORI:
Tempo di processo più breve, solo 15 minuti
Arrotondamento simmetrico e uniforme
Risultati affidabili e ripetibili
Rimozione di sbavature senza residui
Leggera deviazione di forma sulle superfici di pressione della scanalatura di abete
Conformità sicura e misurabile con tolleranze molto basse inferiori a 1 µm
Rimozione puramente meccanica: nessun utilizzo di acceleratori di processo chimici
COME FUNZIONA STREAMFINISH?
Nel processo Streamfinish sviluppato da OTEC, i componenti come dischi di turbina o pale di turbine o compressori vengono bloccati in un supporto e immersi in un contenitore rotante riempito con agenti abrasivi o lucidanti (materiali di finitura). I pezzi possono anche essere messi in rotazione o posizionati nel flusso ad angoli definiti.
Il conseguente movimento relativo che si genera tra il componente e i materiali di esercizio garantiscono una lavorazione omogenea. Grazie alle enormi forze di lavoro fino a 9 tonnellate, è possibile lavorare la superficie in maniera più efficace e più rapida rispetto a qualsiasi altro metodo di finitura superficiale. A seconda delle dimensioni, delle condizioni iniziali e della preparazione del componente (ad es. smussatura dei bordi), è possibile ottenere un raggio fino a 700 µm entro 15 minuti. Grazie alla grana molto fine del materiale di finitura, questo arrotondamento può essere eseguito anche su geometrie com-plesse e di difficile accesso.
Le macchine di finitura a flusso con automazione integrata per componenti grandi e pesanti sono disponibili solo da OTEC: i pezzi con un diametro fino a 650 mm e un peso fino a 200 kg possono essere lavorati dalla SF-HP di nuova concezione.
DEFINIZIONE DEL PROCESSO IDEALE CON GLI ESPERTI OTEC PRÄZISIONSFINISH
Anche i componenti con requisiti di post-produzione altrettanto elevati traggono vantaggio dall'uso della tecnologia OTEC Streamfinish. Questi includono, ad esempio: dischi di turbine e compressori, piedini della pala di turbina, blisk, servovalvole, ingranaggi, dadi a sfere o componenti del telaio. Indipendentemente dalla geometria e dai requisiti per la qualità della super-ficie o l'arrotondamento, il team di esperti del Centro di finitura OTEC è al tuo fianco per individuare il tipo di processo. In-sieme troveremo il processo più adatto per il tuo componente. Prendi subito un appuntamento per essere presente di perso-na o digitalmente durante la finitura del tuo campione.

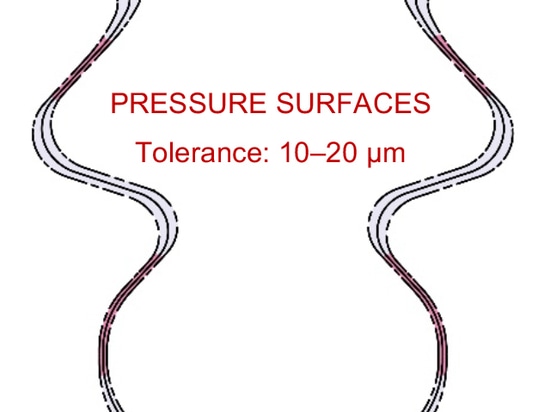