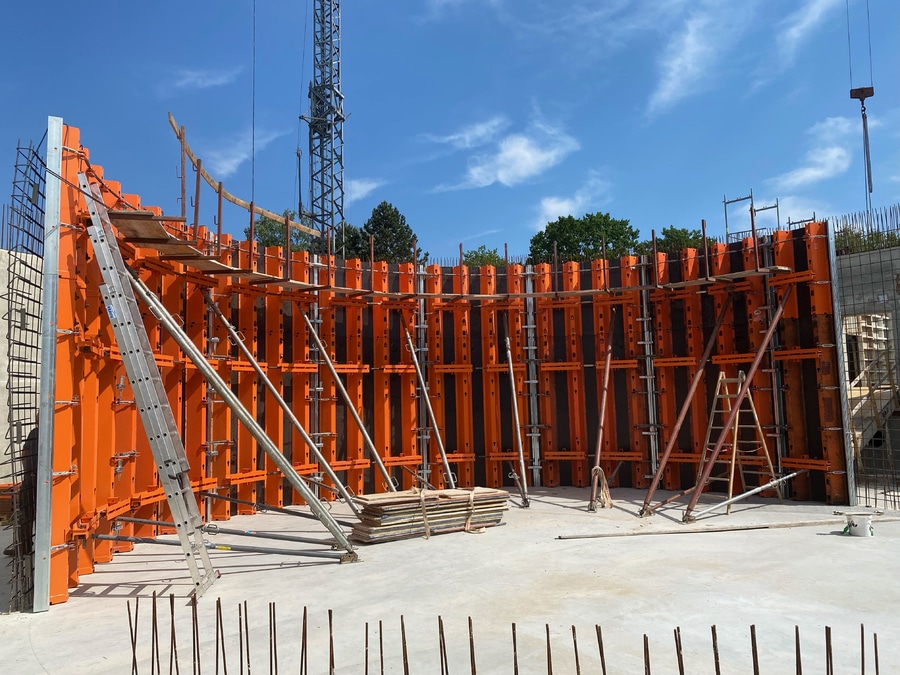
Vedi traduzione automatica
Questa è una traduzione automatica. Per vedere il testo originale in inglese cliccare qui
#Tendenze
{{{sourceTextContent.title}}}
"Cassaforma ad alta velocità": con morsetti al posto dei bulloni
{{{sourceTextContent.subTitle}}}
La cassaforma per il nucleo interno di un serbatoio per l'acqua potabile dell'acquedotto di Schönewörde è stata realizzata in tempi brevissimi grazie alla cassaforma a travi trapezoidali circolari con collegamento a morsetto di PASCHAL.
{{{sourceTextContent.description}}}
Quando Mathias Müller, consulente specializzato in casseforme nella filiale PASCHAL di Gifhorn, guarda fuori dalla finestra, vede l'edificio degli uffici del Gifhorn Water Board. Il Gifhorn Water Board ha sette acquedotti che assicurano la fornitura di acqua potabile ai 128.000 abitanti di sette comuni e delle città di Gifhorn e Wittingen, nello stato tedesco della Renania Settentrionale-Vestfalia. L'impresa di costruzioni Baugeschäft Gruska sta costruendo un nuovo serbatoio di acqua potabile per uno di questi, l'acquedotto di Schönewörde. L'attuale serbatoio ha bisogno di essere rinnovato dopo tre decenni di servizio. L'impresa edile di Salzwedel aveva già costruito un serbatoio per l'acqua potabile a Wittingen tre anni fa, utilizzando le soluzioni di casseratura di PASCHAL. PASCHAL ha fornito anche gli elementi dei pannelli per questo lavoro. Con un'innovazione: I collaboratori di Axel Gruska hanno utilizzato per la prima volta la cassaforma per travi trapezoidali circolari con collegamento a morsetto (TTK), presente sul mercato dal 2013 circa.
PASCHAL è stato commissionato a maggio e gli elementi in pannelli, realizzati a mano nella sede dell'azienda nella Foresta Nera, sono stati consegnati il 5 giugno. L'ordine era di circa 150.000 euro. L'ordine complessivo per la costruzione del serbatoio di acqua potabile è stato di circa 1,8 milioni di euro.
Due semicerchi - due passi
Il nucleo interno del serbatoio per l'acqua potabile da formare è stato progettato e realizzato in due sezioni di cassaforma. In totale, l'area da casserare misurava 320 metri quadrati. Poiché si trattava di due sezioni, Gruska Baugeschäft ha dovuto noleggiare elementi di cassaforma per soli 160 metri quadrati: una soluzione economicamente vantaggiosa. Il consulente specializzato in casseforme Mathias Müller spiega: "In primo luogo, è stato formato un semicerchio e gettato in calcestruzzo. Poi la cassaforma è stata spostata e si è formato il secondo semicerchio. Le due sezioni di calcestruzzo sono state poi collegate tra loro. Il cliente ha avuto bisogno di meno casseforme, il che è stato vantaggioso in termini di costi"
2 minuti invece di 15: montaggio rapido grazie alla connessione a morsetto
La cassaforma per un semicerchio era composta da sette singoli segmenti che sono stati ulteriormente sollevati per raggiungere un'altezza complessiva di 4,50 metri. Il grande vantaggio di TTK: i singoli elementi dei pannelli possono essere assemblati più rapidamente grazie ai morsetti.
"Con la precedente cassaforma circolare, erano necessari 15 bulloni per collegare tra loro due pannelli di cassaforma con un'altezza di 450 cm. Ora è sufficiente posizionare quattro morsetti e non è più necessario infilare i bulloni nei fori", spiega Mathias Müller. Per dirla più semplicemente: "Colpisci con un martello e il gioco è fatto!" Anche Axel Gruska ha confermato che il posizionamento dei morsetti è stato veloce. Le connessioni a morsetto hanno permesso a quattro dipendenti dell'impresa di costruzioni di allestire i segmenti di cassaforma per una sezione in due giorni. O, per dirla diversamente: Se ci volevano circa 15 minuti per posizionare i bulloni per collegare due segmenti di cassaforma tra loro, ora ci vorranno solo circa due minuti.
Non è necessario alcun aggiustamento
Il raggio di un oggetto circolare da casserare può essere preimpostato al centimetro esatto con TTK. I bordi della cassaforma sono stati pre-arrotondati per Gruska Baugeschäft nella filiale di Gifhorn. "Anche questo è incluso nel nostro pacchetto di servizi", afferma Müller, aggiungendo: "I dipendenti dovevano solo impostarle e assemblarle nell'acquedotto. Altrimenti, uno di essi potrebbe differire di mezzo centimetro durante la produzione manuale degli elementi in legno" Il caposquadra Jan Müller ha confermato che "tutto si è montato perfettamente al primo colpo" In questo caso non è stata necessaria alcuna regolazione.
Il collega di Müller nell'ufficio PASCHAL di Gifhorn era responsabile della progettazione della cassaforma. Iwan Weber l'ha realizzata sulla base del piano di casseratura dello studio di ingegneria Scholz di Brunswick. Una volta consegnata la cassaforma, Mathias Müller si è recato personalmente sul posto e ha fornito a Jan Müller istruzioni e suggerimenti sulla gestione della cassaforma: ad esempio, ha spiegato quanti morsetti dovevano essere fissati in altezza per evitare deviazioni verticali.
L'impresa di costruzioni ha inoltre beneficiato di brevi distanze di trasporto grazie alla vicinanza reciproca. La cassaforma è stata utilizzata in totale per tre settimane, un periodo più breve del previsto. Anche il supporto professionale è un fattore importante. "Il signor Müller è un consulente eccellente, in grado di comunicare tutto ciò che avviene in cantiere in modo facile da capire e di garantire che tutto funzioni", afferma Axel Gruska.
Niente olio per casseforme
Un vantaggio che si è rivelato evidente è che l'impresa di costruzioni è stata rifornita di materiale per casseforme come nuovo direttamente dall'officina della sede centrale di PASCHAL a Steinach. La cassaforma a travi trapezoidali circolari non era mai stata utilizzata in precedenza in un cantiere. "Normalmente, il compensato viene oliato per facilitare la rimozione della cassaforma dal calcestruzzo", ha spiegato Mathias Müller, aggiungendo: "Ma non si può usare l'olio per le vasche di cemento che contengono acqua potabile. Questo ovviamente rende un po' più difficile il successivo lavoro di pulizia" I dipendenti del cantiere che hanno rimosso la cassaforma dopo che il calcestruzzo si era solidificato non hanno avuto alcun problema durante il disarmo della nuova cassaforma.
"La finitura del calcestruzzo era perfetta", ha commentato il capo dell'impresa di costruzioni.
Acqua spenta - da gennaio 2024
Il serbatoio per l'acqua potabile completo avrà un diametro di 22 metri e in futuro potrà contenere 1.500 metri cubi di acqua potabile. Cosa resta da fare: I macchinari devono essere installati, tutte le tubature devono essere posate e la sala operatoria deve essere costruita. Il cerchio interno funge da cosiddetto muro di guida. L'acqua viene pompata al centro e distribuita attraverso il flusso; l'acqua viene sifonata dall'area esterna della vasca per essere immessa nel sistema di tubature. Il serbatoio viene poi sigillato con un coperchio. L'entrata in funzione della struttura è prevista per l'inizio del 2024. In seguito, il serbatoio di acqua potabile esistente potrà essere ristrutturato e servirà come riserva.
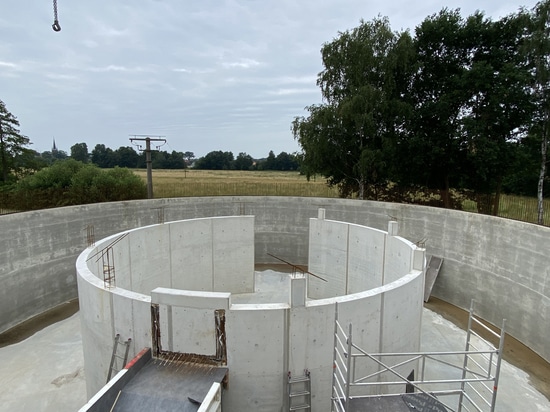
{{medias[189671].description}}
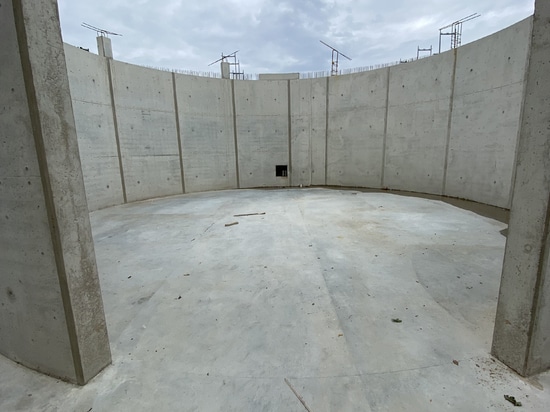
{{medias[189672].description}}

{{medias[189673].description}}