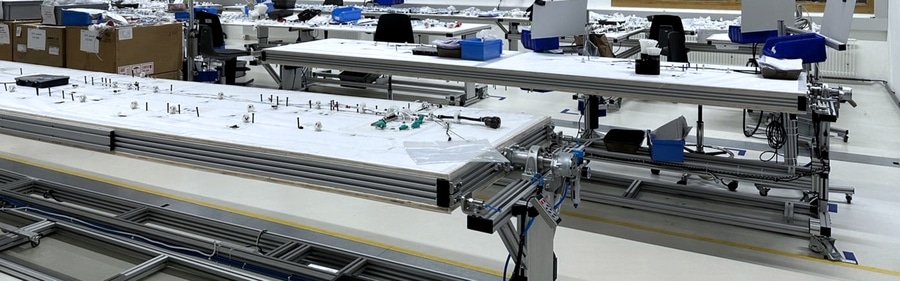
Vedi traduzione automatica
Questa è una traduzione automatica. Per vedere il testo originale in inglese cliccare qui
#News
Tempi di cambio ridotti con tavoli di assemblaggio modulari
Tempi di cambio ridotti con tavoli di assemblaggio modulari ed ergonomici realizzati con profili in alluminio
Situazione iniziale:
L'azienda svizzera Pilatus Aircraft Ltd, attiva a livello internazionale, è nota per i suoi velivoli unici a livello mondiale, come gli aerei da addestramento e i piccoli velivoli multiuso. Per i diversi velivoli sono necessari vari cablaggi, che differiscono notevolmente in termini di design, come la lunghezza e la forma. A seconda del design del cablaggio, sono state allineate semplici tavole nella forma richiesta e sono state montate le schede appropriate. Sebbene questo metodo funzionasse in linea di principio, rendeva difficile lavorare in modo comodo e sicuro. Da un lato, si urta contro le gambe del tavolo quando si lavora e, dall'altro, non è possibile assumere una postura comoda ed ergonomica. Inoltre, il posizionamento dei tavoli è scomodo e richiede molto tempo.
La sfida:
L'obiettivo di Pilatus era quello di ottenere un sistema di postazioni di lavoro che aumentasse l'ergonomia e la sicurezza dei dipendenti, ma che allo stesso tempo fosse modulare e adattabile in modo flessibile ed espandibile in qualsiasi momento. Anche i tempi di sostituzione dei tavoli e delle schede per l'installazione dei vari cablaggi dovevano essere ridotti e semplificati. Per la conversione delle grandi superfici di lavoro non dovrebbero essere necessari più di due addetti.
Soluzione:
Phoenix Mecano ha lavorato a stretto contatto con KKS Ultraschall AG per sviluppare una proposta di progettazione personalizzata. Questa collaborazione si è basata su una partnership di lunga data e su una profonda comprensione delle condizioni specifiche di KKS Ultraschall AG. Con l'aiuto dei file STEP forniti, il cliente è stato in grado di ottenere una visione dettagliata e di apportare le necessarie modifiche prima della produzione finale della copertura della macchina, il che ha reso il processo di sviluppo particolarmente efficiente. L'eccellente comunicazione e la comprensione reciproca hanno reso la collaborazione molto più semplice. Anche le piccole modifiche sono state implementate in modo rapido ed efficiente, a sostegno dell'intero processo di sviluppo. Phoenix Mecano ha tenuto conto anche di requisiti speciali come la conformità alle norme e l'uso di profili chiusi. Dopo il completamento, Phoenix Mecano ha organizzato il trasporto dell'involucro della macchina a KKS Ultraschall AG, con una consegna modulare a causa delle dimensioni dell'involucro della macchina. Questa modularità ha facilitato il montaggio in loco e ha garantito una perfetta integrazione con il sistema di incisione e pulizia. Inoltre, Phoenix Mecano ha fornito a KKS Ultraschall AG uno spazio di stoccaggio per risolvere eventuali problemi di spazio in modo flessibile ed efficiente.
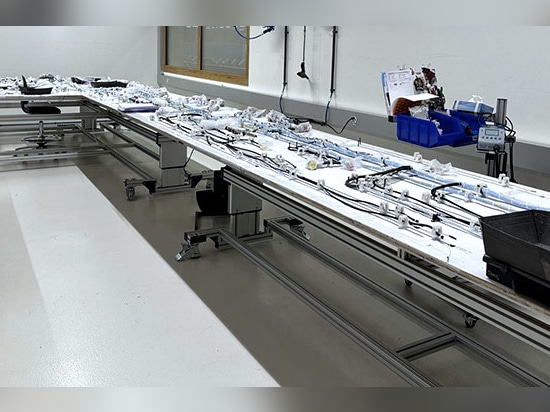