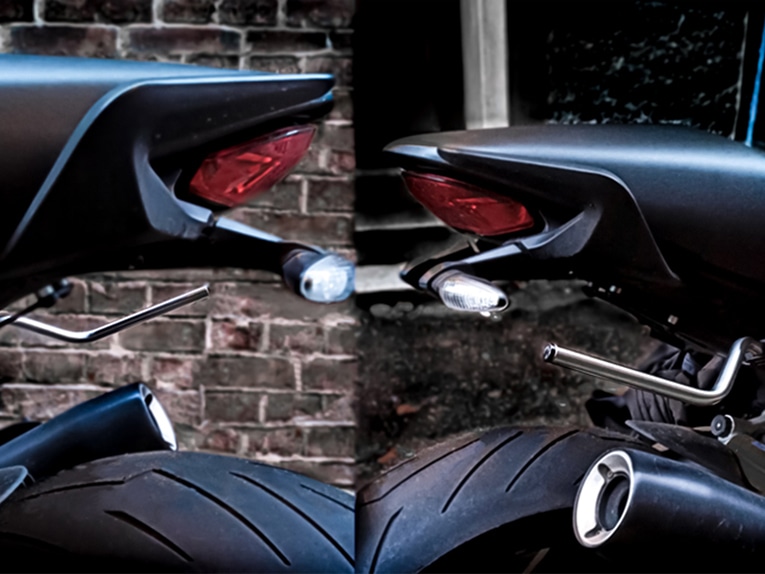
Vedi traduzione automatica
Questa è una traduzione automatica. Per vedere il testo originale in inglese cliccare qui
#Tendenze
Ricambi per una moto: dalla scansione 3D alla stampa 3D
Aggiornamento moto con il flusso di lavoro Scan-Design-Print di SHINING 3D
Con la tecnologia 3D, la comunità globale di produttori, progettisti professionisti e ingegneri ha fatto nascere gadget fantastici. In qualità di azienda sempre alla ricerca dell'eccellenza nei settori della scansione 3D, della progettazione intelligente e della stampa 3D, il nostro obiettivo è quello di ispirarvi con un bouquet di idee straordinarie che anche voi potrete utilizzare per migliorare la vostra vita quotidiana in modo efficiente! Nel caso di oggi esaminiamo il processo di sostituzione di un pezzo di ricambio di una moto che è stato riprodotto in modo più veloce e molto più economico con le tecnologie dalla scansione alla stampa, alimentate da SHINING 3D!
Non è comodo, quando si parte per un viaggio, avere tutto il necessario a portata di mano senza bisogno di usare una grande valigia? Due tubi d'acciaio assialsimmetrici sono incollati su un supporto su una motocicletta che compone un portabagagli e permettono di montare i bagagli sul retro del veicolo. Purtroppo uno di questi tubi è andato perso durante la guida, quindi per continuare il viaggio di convenienza è necessario sostituirlo. Abbiamo affrontato questo problema con la scansione 3D e la stampa 3D del metallo, tecnologie con le quali SHINING 3D mira a migliorare e aggiungere valore alla vita di molti.
PASSO 1: SCANSIONE 3D
La scansione 3D è una disciplina che può ancora essere considerata come un suggerimento segreto estremamente efficiente nella catena del flusso di lavoro additivo, perché può sostituire i complessi processi di progettazione e facilitare lo sviluppo di prodotti in dimensioni innovative. Nel nostro caso, il nuovo scanner 3D portatile ibrido leggero EinScan HX viene utilizzato per digitalizzare il tubo d'acciaio di sinistra. Gli scanner 3D EinScan rendono popolare l'applicazione della più recente tecnologia di scansione 3D e la rendono accessibile ai professionisti, ai creativi e agli hobbisti a casa. Dopo il processo di scansione, un file STL viene esportato dal software EXScan Pro, aprendo la strada alla fase successiva della catena del flusso di lavoro additivo.
FASE 2: PROGETTAZIONE INTELLIGENTE
Il file STL esportato da EXScan Pro viene importato nel software Voxeldance Additive, un software di preparazione dati che aiuta a risparmiare tempo di produzione e ad ottimizzare il flusso di stampa. La geometria della superficie grezza dell'STL viene riparata e chiusa in un modello a tenuta stagna utilizzando il modulo di fissaggio. Poiché i due tubi d'acciaio che compongono il supporto del bagaglio sono assialsimmetrici, la parte scansionata viene specchiata attorno a due assi per generare le caratteristiche originali della parte mancante. Poiché in questo caso vogliamo sottolineare l'eccezionale valore che la tecnologia digitale 3D può aggiungere soprattutto nel campo della produzione, abbiamo deciso di stampare il tubo in 3D con un materiale molto più leggero di quello originale. La lega di alluminio AlSi10Mg utilizzata, pesa solo 2/3 dell'acciaio inossidabile di cui è fatta la parte originale.
Per creare una parte ancora più forte di quella originale, viene utilizzato il Structure-Tool of Voxeldance Additive. Questa procedura facile da usare aiuta a scavare la parte, a creare una struttura reticolare altamente variabile e ad aggiungere fori di colata per rimuovere la polvere non fusa all'interno della barra. Avere tutte queste preziose caratteristiche combinate in un unico software rende Voxeldance Additive un potente strumento per la preparazione dei dati di stampa 3D.
FASE 3: PRODUZIONE ADDITIVA
Le parti ottimizzate vengono poi fuse nella realtà dalla stampante 3D a doppio laser metallico 3D EP-M250 Pro. Per una facile rimozione delle parti stampate dalla piattaforma di costruzione, la struttura di supporto è stata progettata utilizzando il software di preparazione Voxeldance Additive. Con la funzione di supporto automatico, uno script di parametri di supporto predefinito ma altamente regolabile viene utilizzato per creare il supporto in modo perforato e frammentato, ma abbastanza forte da mantenere le parti in posizione. Dopo 4,5 ore e mezzo di fusione delle particelle metalliche insieme, i due tubi possono essere facilmente rimossi dalla piattaforma con le mani e le pinze.
FASE 4: POST-ELABORAZIONE
Per ottenere una superficie liscia e un buon aspetto generale, la post-elaborazione è fondamentale. Nella parte inferiore del pezzo, la struttura di supporto viene rimossa con pinze e lime. L'uso di carta vetrata e di una sabbiatrice con corindone bianco conferiscono al pezzo la perfetta finitura opaca.
ANALISI DELLA REDDITIVITÀ
Combinando tutti i fattori di costo in questo processo, come la manodopera, le materie prime, l'elettricità, l'usura delle macchine e i costi dei locali, si raggiunge un totale di 184€ per entrambi i bar. L'OEM offre solo l'acquisto di un intero set del sistema di bisaccia per 310€. L'uso della stampa 3D in metallo ha contribuito a ridurre il peso del supporto della bisaccia da 525 g a 86 g, con una riduzione di peso dell'83% e un aumento della stabilità grazie alla progettazione di strutture di supporto integrate all'interno dei tubi.
Se volete saperne di più sul flusso di lavoro digitale di Shining 3D o avete bisogno di aiuto per calcolare i costi totali della vostra stampa, contattateci oggi stesso! Siamo entusiasti di aiutarvi a risparmiare tempo, materiale e denaro - per altre idee brillanti!