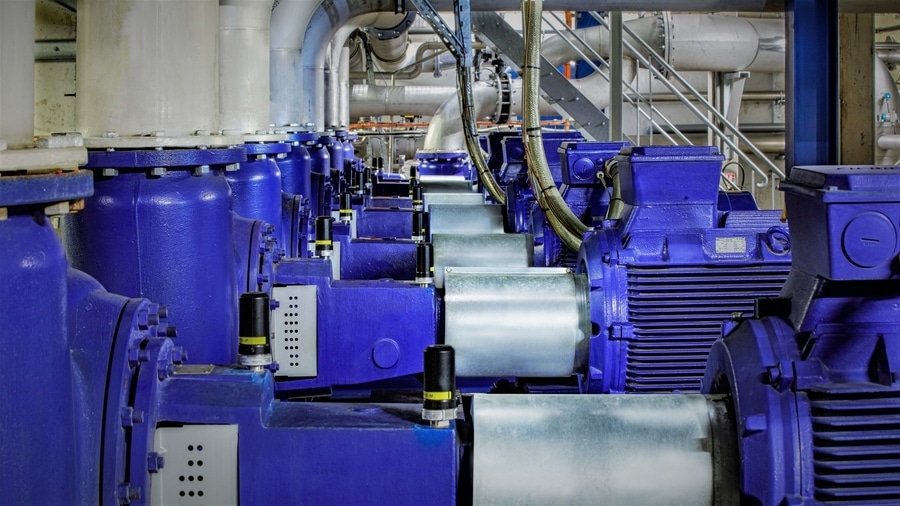
#Tendenze
Le risorse meccaniche imparano a parlare
Dalla manutenzione preventiva a quella predittiva
Il monitoraggio continuo delle condizioni della macchina può rendere le operazioni più sicure ed efficienti. Soprattutto per i componenti critici, la manutenzione basata sulle condizioni o addirittura predittiva è oggi il metodo di scelta: apparecchiature moderne e intelligenti trasmettono i parametri delle condizioni rilevanti ai sistemi di gestione della manutenzione di livello superiore. Ma per quanto riguarda le risorse più vecchie senza capacità diagnostiche? Qui, una combinazione ben progettata di sensori IIoT, unità gateway e servizi cloud offre una soluzione di retrofit ideale. In un centro di produzione di strumentazione di processo e analisi, questo pacchetto si rivela estremamente conveniente e versatile.
Per decenni, i team di manutenzione negli impianti di processo e di produzione hanno cercato di aumentare la produttività complessiva dell'impianto. Un elemento chiave di questo sforzo è lo sviluppo e l'implementazione di efficaci strategie di manutenzione. L'approccio tradizionale di far funzionare le apparecchiature fino a quando non si guasta (noto come "run to failure") si è da tempo dimostrato di essere inefficiente e costoso. Un passo importante nello sviluppo di strategie di manutenzione più efficaci è stata l'introduzione della manutenzione preventiva (PM). Si riferisce alle attività di manutenzione ordinaria e di ispezione che vengono eseguite secondo programmi definiti. Tuttavia, mentre il PM aiuta a prevenire guasti imprevisti, comporta anche una manutenzione non necessaria quando l'apparecchiatura è in buone condizioni.
Il passo successivo nello sviluppo di strategie di manutenzione efficienti è la manutenzione predittiva (PdM). Ciò comporta la raccolta e l'analisi dei dati sulle condizioni delle apparecchiature per prevedere quando potrebbe essere necessaria la manutenzione. L'obiettivo è eseguire la manutenzione quando è necessaria, in base alle condizioni effettive dell'apparecchiatura piuttosto che a un programma prestabilito. Un aspetto chiave del PdM è il Condition-Based Monitoring (CBM), il monitoraggio continuo e l'analisi delle condizioni delle apparecchiature durante il normale funzionamento. L'implementazione di successo della manutenzione basata sulle condizioni richiede una serie di tecnologie e risorse, inclusi sensori adeguati, sistemi di trasmissione e elaborazione dei dati e software di analisi specializzato. Senza queste risorse, è impossibile eseguire la manutenzione in base alle condizioni attuali della macchina. Il retrofit di tali tecnologie è ora possibile a basso costo per apparecchiature rotanti o vibranti, come illustra il seguente esempio.
Competenza nella produzione di misuratori di portata
Lo stabilimento Siemens di Haguenau, in Francia, che ha celebrato il suo 50° anniversario nel 2020, impiega oltre 800 persone. Specializzato nella produzione di trasmettitori di pressione, misuratori di portata e analizzatori di gas, lo stabilimento è stato riconosciuto per il suo approccio innovativo alla trasformazione digitale: dal 2015, lo stabilimento ha continuamente ottimizzato la sua produzione attraverso l'automazione, la robotica e la digitalizzazione. I processi di produzione possono ora essere simulati in tempo reale e resi più efficienti.
Qui, Robert Gerber coordina la manutenzione, mentre il suo collega David Uhrig è responsabile della pianificazione dell'assistenza. "In termini di manutenzione, negli ultimi anni abbiamo fatto passi da gigante", afferma Uhrig, che lavora presso lo stabilimento di Haguenau dal 1995, prima come tecnico di manutenzione e poi come pianificatore della manutenzione: "I nostri team di manutenzione aiutano a garantire che l'efficienza delle piante migliora anno dopo anno. Monitoriamo le apparecchiature di produzione 24 ore su 24 e ora beneficiamo di capacità diagnostiche che le apparecchiature non avevano alcuni anni fa. Le strategie di manutenzione variano da sezione di impianto a sezione di impianto”, come riferisce Gerber: “Immagino si possa dire, siamo nell'area di tensione tra il volerlo fare e il poterlo fare quotidianamente: da un lato, sappiamo dalle analisi di criticità quali parti dell'impianto hanno quali effetti sulle prestazioni operative in caso di guasto ea cosa dobbiamo prestare particolare attenzione. D'altra parte, non possiamo sviluppare strategie di manutenzione predittiva per tutti gli asset perché non abbiamo i dati sulle condizioni".
I pezzi di ricambio sono disponibili per le apparecchiature più critiche, ma ciò non è sufficiente per prevenire i tempi di inattività: "Prendete la nostra autoclave, ad esempio", spiega Gerber: "Tutti i misuratori di portata hanno uno speciale rivestimento interno che viene vulcanizzato nell'autoclave. Se fallisce, la produzione si ferma. Il motore per il soffiatore dell'autoclave è fondamentale, quindi lo teniamo in magazzino. Il problema con un guasto improvviso è che la ventola è montata sull'albero motore senza giunto. Ci vogliono due giorni di lavoro e l'impiego di specialisti, anche se abbiamo il ricambio a magazzino”.
Monitoraggio basato sulle condizioni per il retrofitting
I due specialisti della manutenzione desideravano un'opzione di monitoraggio basata sulle condizioni per questo motore e hanno trovato ciò che stavano cercando internamente: Sitrans Smart Condition Monitoring IQ (SCM IQ), sviluppato da Siemens AG, è un sistema intelligente per il monitoraggio continuo e la manutenzione di componenti rotanti o vibranti della macchina. Utilizza una combinazione di sensori IIoT e intelligenza artificiale per registrare e analizzare continuamente i dati di vibrazione e temperatura.