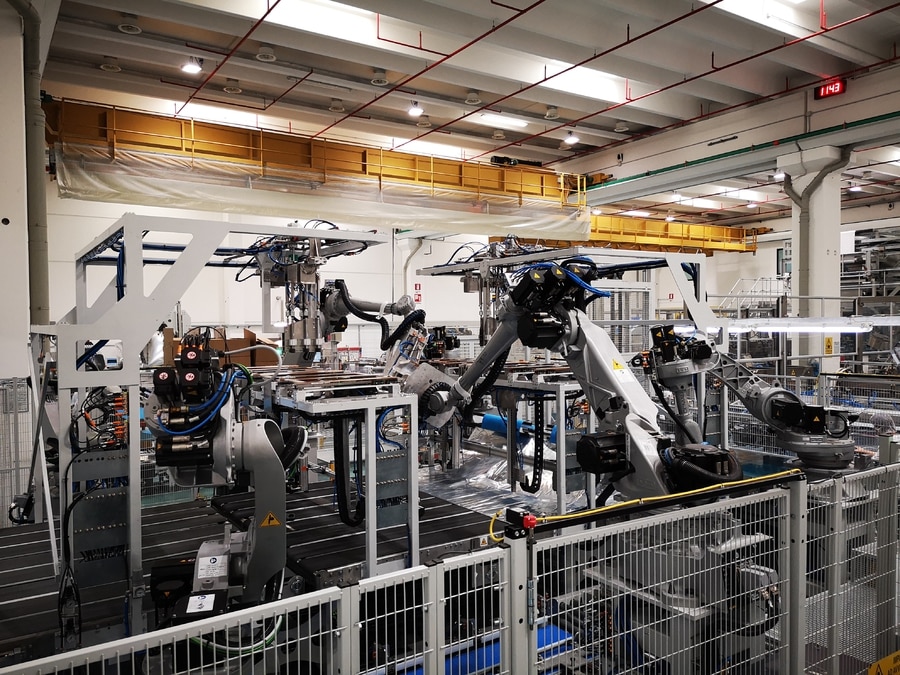
#News
Automazione spinta nel campo dell’imballaggio flessibile
Robot antropomorfi Comau per la piegatura multipla di sacchi
Nello stabilimento Goglio, situato a Daverio in provincia di Varese, è attivo un sistema che utilizza robot antropomorfi Comau per la piegatura multipla di sacchi dotati di bocchettone di riempimento prodotti in film multistrato, e per l'imballaggio ottimizzato degli stessi in scatole di cartone con apposita busta igienica interna. L’impianto, che contiene molti elementi tecnologicamente innovativi, è stato progettato dall’integratore Siscodata
Goglio è un leader mondiale nel settore dell’imballaggio flessibile. L’azienda, fondata nel 1850 e ancora oggi in mano alla famiglia Goglio, ha conosciuto nel corso degli anni una costante crescita basata su investimenti in sistemi di produzione innovativi e sempre più automatizzati. I clienti di Goglio sono le aziende trasformatrici di tutto il mondo operanti in svariati settori industriali quali il Caffè, Asettico & Hot Filling, Piatti pronti, Alimentari, Cosmetica e Detergenza, Beverage, Sostanze industriali e Pet Food.
Il modello di business di Goglio è racchiuso nel marchio registrato Fres-co System, nato nel 1961, che identifica l’obiettivo dell’azienda: realizzare sistemi per la conservazione e il mantenimento degli alimenti freschi come appena prodotti. All’interno del Sistema Goglio si trova un’offerta completa composta da laminati flessibili alta barriera, linee di confezionamento, accessori plastici, assistenza tecnica e servizio.
Goglio, con la propria attività, è costantemente impegnata a offrire soluzioni che aiutino a garantire cibo sano, sicuro e sufficiente per tutti, nel rispetto del pianeta e dei suoi equilibri. Per raggiungere questi livelli di affidabilità del prodotto, l’azienda ha puntato sulla verticalizzazione spinta del processo produttivo, come ci spiega Luigi Foglia, direttore di produzione della Aseptic & Industrial Bags, divisione Packaging: «Produciamo praticamente quasi tutto all’interno dei nostri stabilimenti, questo per avere il totale controllo della qualità dei nostri prodotti. Nella produzione di un sacco asettico, per esempio, compriamo da fornitori esterni film come poliestere, nylon alluminio mentre tutto il resto, compresi valvole e bocchettoni unitamente alla grafica sui sacchi, viene realizzato internamente. Questa scelta richiede ovviamente una perfetta organizzazione in grado di gestire in tempi rapidi anche eventuali prodotti che non vanno bene».
Goglio può a buon diritto considerarsi un’azienda globale avendo ben 8 sedi produttive nel mondo e 7 sedi commerciali. In totale, l’azienda conta 1754 dipendenti di cui 992 in Italia.
Nel nostro paese, oltre alla sede di Daverio, in provincia di Varese, dove si trovano il quartier generale, la divisione Imballaggi e Polimeri e il Technology Center, vi sono le sedi di Milano (divisione Plastica), Zeccone (dove vengono prodotte le macchine) e Cadorago (divisione Cofibox).
All’estero, Goglio ha una sede produttiva in Olanda, dove si producono imballaggi flessibili, due sedi negli Stati Uniti, in cui si producono imballaggi flessibili, macchine e accessori plastici, e una sede cinese a Tianjin dove si realizzano imballaggi flessibili e macchine.
Con riferimento agli Usa, Luigi Foglia sottolinea che: «… le due società negli Stati Uniti sono cresciute in sinergia con Starbucks, la famosa catena di caffè statunitense unica nel suo genere. Anni fa, infatti, il management Goglio credette in questo progetto e da allora le due aziende si sono sviluppate in maniera esponenziale grazie alla reciproca collaborazione».
Nel 2018, il gruppo ha fatturato 375 milioni di euro, quasi il 50% del quale riferito al settore Caffè, seguito dai comparti Asettico (19,1%), Prodotti Industriali (11%), Alimentari (9,6%) e via via gli altri. La produzione di macchine ammonta a circa il 9% del fatturato.
Automazione come sinonimo di crescita
«L’automazione è sempre stata nel DNA di Goglio. Per noi automatizzare significa efficientare i sistemi produttivi, ridurre i costi di produzione, consentire al nostro personale di svolgere mansioni a più alto valore aggiunto, come quella, per esempio, del controllo di qualità» premette Luigi Foglia.
Da questo presupposto nasce l’applicazione che ha visto coinvolti, oltre all’azienda di Daverio, Comau e il system integrator Siscodata Computer Srl di Arcisate in provincia di Varese, un’azienda con sede ad Arcisate (VA) specializzata nella realizzazione di sistemi robotizzati in molteplici comparti industriali.
Nello specifico, Goglio si è rivolta a Siscodata per la realizzazione di un impianto robotizzato che risolvesse i problemi di produzione, piegatura e inserimento manuale di sacchi dotati di bocchettone di riempimento prodotti in film metallizzato, materiale che di per sé stesso è scivoloso e le cui dimensioni maggiorate, nel corso degli anni, non consentivano più l'utilizzo delle precedenti piegatrici.
«Per la produzione manuale di questi sacchi impiegavamo una piegatrice/faldatrice progettata per la piegatura delle lenzuola, la cui misura massima, si sa, è riferita a un letto matrimoniale. A monte della faldatrice, alcune operatrici completavano l’operazione inserendo le confezioni all’interno delle scatole dotate di apposita busta igienica interna. Per le confezioni di grosse dimensioni, il lavoro veniva svolto in modo totalmente manuale» ci spiega Luigi Foglia.
La necessità di Goglio, quindi, non era solo quella di automatizzare il processo, bensì anche avere a disposizione un unico impianto in grado di passare in maniera rapida da confezioni di 220 litri a doppio canale (1x1,8 metri di dimensione), a confezioni da 1-1,5 t (2,2x2,6 m di dimensione) a cui vengono applicate due differenti tipi di valvole, rispettivamente da 1” o 2”.
Serviva pertanto un sistema per automatizzare la fase di piegatura e arrotolamento di queste tipologie di sacchi e di inscatolamento sfalsato degli stessi ad alta velocità.
Siscodata, in collaborazione con Comau, ha così progettato un’isola robotizzata composta da 4 robot antropomorfi Comau modello NS16, da 16 kg di portata al polso e1,65 m di sbraccio e 2 NJ40, con 2,5 m di sbraccio, che si occupano delle piegature trasversali secondarie e del confezionamento all’interno della scatola.
I robot sono posizionati su base di acciaio in connessione a un formatore di cartoni con busta igienica interna in film e nastratrice a chiusura.
I 4 robot addetti alla piega sono dotati di un’apposita pinza di prelievo dei sacchi in arrivo distesi sul nastro trasportatore di ingresso, che dispone anche di un accatastatore e di un allineatore dei bocchettoni che vengono inseriti prima della piega
I sacchi, in arrivo sul nastro trasportatore in coppia o singolarmente se di grandi dimensioni, vengono prelevati da 2 robot (uno per parte), arrotolati e piegati. Le due coppie di robot NS16 si alternano nel lavoro per garantire l’elevata velocità. Il robot deposita poi il sacco piegato in una stazione di accumulo dove gli altri due altri robot prelevano il singolo sacco e lo depositano piegandolo trasversalmente nella scatola già formata con il film di protezione. Terminato il riempimento, la scatola viene chiusa con nastro adesivo grazie alla nastratrice. Il deposito nella scatola è continuamente sfalsato e alternato (sopra/sotto, destra/sinistra) per compensare i bocchettoni di plastica e ottimizzare il volume della scatola.
Il numero di sacchi in una scatola è passato dai 36 del processo manuale ai 42/44 pezzi con un significativo risparmio di volume nella fase di spedizione.
«Insieme a Siscodata abbiamo definito i modelli di robot Comau più adatti per questa applicazione – dice Giulio Scifo, sales account di Comau in Italia. La particolarità delle due coppie di robot NS16 è che lavorano in modo cooperativo grazie a un unico armadio di controllo che consente, inoltre, di risparmiare spazio e costi di duplicazione dell’hardware.
Ciò è evidente dal fatto che i due robot arrotolano con un perfetto sincromismo le buste che arrivano tramite il nastro».
L’impianto lavora con un tempo ciclo molto sostenuto (una busta ogni 6 secondi) e questo ha richiesto delle soluzioni progettuali che hanno impegnato non poco i tecnici di Comau e Siscodata. Due le principali difficoltà: impiegare robot antropomorfi con basso payload per avere alte velocità; realizzare una pinza leggera per arrotolare i sacchi con aste lunghe più di un metro.
Il punto cardine del progetto è stato quindi lo studio e la realizzazione della pinza di presa, arrotolamento e piegatura.
«L’esigenza di far lavorare l’impianto a elevate velocità ha condizionato tutto il progetto nel suo insieme – spiega Roberto Brambilla di Siscodata. Non potendo, pertanto, utilizzare robot con un alto payload al polso, in quanto troppo pesanti e quindi troppo lenti per movimentare i carichi in gioco, la nostra attenzione si è concentrata sullo sviluppo della pinza, caratterizzata da uno sbraccio di circa 1,2 m, che doveva essere contemporaneamente rigida e leggera. Per la sua realizzazione, è stata fatta una ricerca di materiali tecnici innovativi dopo aver pensato preliminarmente all’acciaio che si è rivelato troppo pesante. Quindi, siamo passati a una lega aeronautica in alluminio che però introduceva seri problemi di flessione verso la parte finale della pinza. La soluzione finale è arrivata puntando sulla fibra di carbonio opportunamente sagomata. Poiché la pinza deve compiere anche una rotazione per l’operazione di arrotolamento abbiamo, inoltre, dovuto aggiungere un addizionale motore brushless come 7° asse rispetto ai 6 canonici del robot Comau standard».
Visibilmente soddisfatto Luigi Foglia spiega che «… Grazie a questo impianto, in funzione dai primi di marzo di quest’anno, abbiamo potuto riprendere a produrre a ciclo continuo, tuttavia non abbiamo ancora raggiunto il regime atteso, attualmente, infatti, possiamo dire di essere al 75% di efficienza produttiva del sistema rispetto al target del 95% in termini di produttività e continuità nell’ambito della giornata lavorativa; siamo comunque confidenti che con l’utilizzo in continuo verranno risolti i problemi di “gioventù” e si raggiungeranno i target prefissati.
Il vantaggio derivante da questo sistema consiste principalmente nell’utilizzo di un numero ridotto di mano d’opera e della riduzione del carico di lavoro gravante sui restanti operatori».
Conclusioni
L’impianto robotizzato installato in Goglio per automatizzare il processo di arrotolamento e piegatura di sacchi cosiddetti BIB (Bag in Box) racchiude molti elementi tecnologicamente innovativi che lo rendono estremamente interessante. Per raggiungere questo risultato, Comau e il suo integratore storico Siscodata hanno lavorato in stretta sinergia interpretando al meglio le esigenze del management dell’azienda di Daverio.
«Per Comau – sottolinea Giulio Scifo – si tratta di un’applicazione molto particolare nel settore della General Industry. Non è la prima volta che il nostro gruppo realizza celle robotizzate con questa densità di robot che si trovano a lavorare in spazi molto ristretti. La maggiore difficoltà, in questo caso, è stata la necessità di far lavorare in continuo i 6 robot in maniera collaborativa con cicli di lavoro particolarmente stressanti».
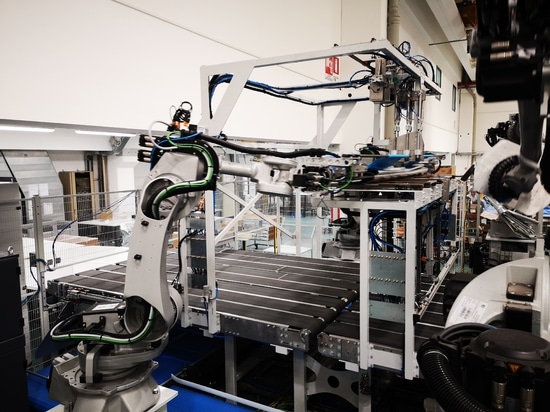