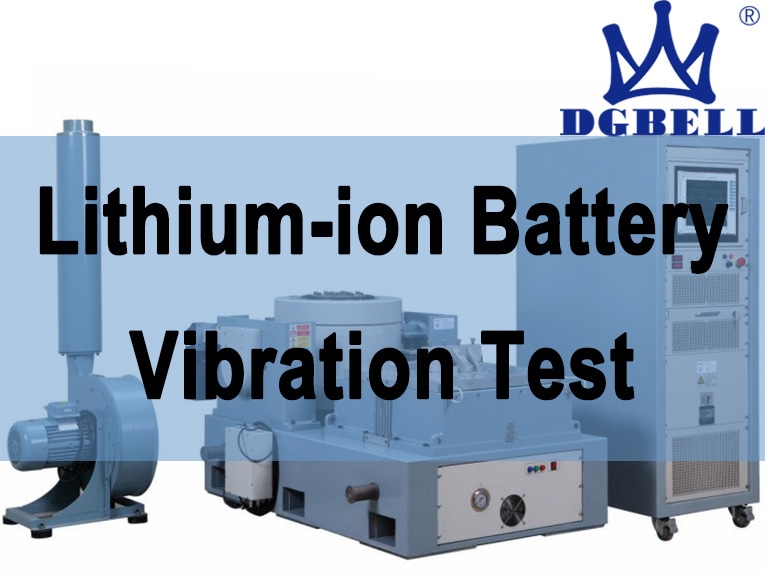
Vedi traduzione automatica
Questa è una traduzione automatica. Per vedere il testo originale in inglese cliccare qui
#News
Test di vibrazione della batteria agli ioni di litio
Test di vibrazione della batteria agli ioni di litio
Le batterie agli ioni di litio comportano rischi per la sicurezza sia nell'aviazione civile e nel trasporto su strada, sia nei trasporti e negli elettrodomestici. Al fine di trovare soluzioni a questi problemi, è stato studiato l'impatto delle vibrazioni meccaniche sulle prestazioni e sul thermal runaway delle batterie agli ioni di litio in condizioni di bassa tensione. In condizioni di bassa tensione, le vibrazioni meccaniche causano un aumento della temperatura di fuga termica delle batterie agli ioni di litio e una variazione significativa del tempo di spegnimento delle valvole di sicurezza.
Le vibrazioni meccaniche a bassa frequenza e di grande ampiezza accelerano il processo di cortocircuito delle batterie, mentre quelle ad alta frequenza aumentano la temperatura di accensione e il volume di scarico delle batterie al litio. Per le batterie agli ioni di litio 18650, la temperatura alla quale la valvola di sicurezza si apre è compresa tra 140 e 150 ℃. Quando la valvola di sicurezza si apre, l'intensità del rilascio di gas è relativamente alta e il segnale di gas può essere una variabile chiave per l'avviso di sicurezza delle batterie al litio. Dopo le vibrazioni a bassa tensione, la capacità di scarica delle batterie agli ioni di litio è inferiore a quella della batteria originale e la velocità di scarica è superiore a quella della batteria originale
1 Tipo di guasto della batteria agli ioni di litio
Essendo il "cuore" di un'auto, le batterie agli ioni di litio determinano la distanza percorsa dall'auto. Il sistema di batterie agli ioni di litio è costituito da quattro componenti principali: moduli batteria (serie di celle singole in parallelo), sistema di gestione della batteria (BMS), sistema di gestione termica e componenti elettrici e meccanici. La funzione principale del BMS è quella di monitorare la tensione, la corrente e la temperatura della batteria in tempo reale attraverso sensori a guscio, attuatori, chip di controllo principali, ecc. Tuttavia, a causa dell'invecchiamento e del decadimento interno di ogni singola batteria del pacco batterie, nonché della corrosione del circuito durante il processo di raggruppamento delle batterie, un funzionamento improprio durante l'uso può portare a fattori esterni anomali, come il sovraccarico e la scarica. L'effetto combinato di questi fattori interni ed esterni porta a guasti interni ed esterni della batteria. I guasti interni delle batterie agli ioni di litio possono essere classificati in tipi come sovraccarico, sovraccarico, cortocircuito interno e fuga termica.
I guasti interni sono causati dal malfunzionamento del BMS e del sensore stesso, che ne impedisce il corretto funzionamento. D'altro canto, sono causati da reazioni elettrochimiche e cortocircuiti interni alla struttura della batteria, con conseguente fenomeno della dendrite di litio. Tuttavia, il pericolo di guasti esterni nelle batterie agli ioni di litio è solitamente maggiore rispetto ai guasti interni. I guasti esterni possono innescare una reazione a catena di guasti interni, portando infine a un riscaldamento incontrollato. I guasti ai sensori sono spesso i più facilmente trascurati, ma possono portare a gravi conseguenze.
Il BMS si affida ai sensori per svolgere funzioni quali il controllo bilanciato, la diagnosi dei guasti e la stima dello stato di carica (SOC). Se il sensore subisce deviazioni, deriva o smette di funzionare, non può ottenere dati in tempo reale e formulare giudizi accurati e ragionevoli sullo stato attuale della batteria. Ciò può non solo ridurre le prestazioni, ma anche causare gravi incidenti di sicurezza. Tuttavia, a causa dell'elevato grado di occultamento dei sensori, la diagnosi è difficile, e questo è anche l'obiettivo e la difficoltà dell'attuale ricerca sui sensori.
Il BMS gestisce pacchi batteria composti da centinaia o addirittura migliaia di singole batterie. A causa delle caratteristiche simili dei guasti delle celle delle batterie, dei guasti dei sensori e dei guasti dei connettori, nonché del fatto che molti guasti sono essenzialmente piccoli e altamente nascosti, è difficile identificarli rapidamente. Di conseguenza, il BMS produce occasionalmente diagnosi e funzionamenti errati. È fondamentale per la sicurezza dell'auto rilevare rapidamente e diagnosticare con precisione i guasti multipli della batteria. Il processo di diagnosi dei guasti della batteria può essere suddiviso grossolanamente in quattro aspetti: rilevamento dei guasti, classificazione dei guasti, localizzazione dei guasti e isolamento dei guasti. L'elaborazione dei dati delle batterie svolge un ruolo fondamentale nella diagnosi dei guasti delle batterie e l'efficacia del denoising può essere verificata efficacemente incorporando metodi matematici di filtraggio morfologico.
2 Problemi con i metodi diagnostici per la misurazione della tensione
(1) Nelle applicazioni pratiche, i sistemi di gestione delle batterie possono misurare solo la tensione ai morsetti di ogni singola batteria del pacco batterie. Per far sì che il valore di misurazione della tensione includa la tensione ai singoli terminali e la tensione sui connettori, è necessario aggiungere ulteriori linee di misura, il che aumenta indubbiamente la complessità dell'apparecchiatura. Se, all'inizio della progettazione del sistema di gestione della batteria, la tensione raccolta comprende la tensione ai morsetti e la tensione sul connettore, il sistema di gestione della batteria non è in grado di ottenere con precisione la tensione ai morsetti della batteria e quindi non è in grado di controllare e gestire efficacemente la carica e la scarica della batteria, con conseguente rischio di errori di sovraccarica e scarica
(2) Le variazioni di tensione causate dalle variazioni della resistenza interna della batteria sono simili alle variazioni di tensione durante i guasti di collegamento Entrambi sono dello stesso ordine di grandezza, quindi i metodi diagnostici basati sui segnali di tensione devono anche affrontare la sfida di distinguere tra i guasti di collegamento e i guasti con aumento della resistenza interna della batteria.
(3) Quando si verifica un leggero allentamento del collegamento all'interno del pacco batteria, l'aumento della resistenza di contatto è molto ridotto. Se la corrente di lavoro del pacco batteria è piccola, un tale difetto di connessione non causerà variazioni significative nel segnale di tensione. Pertanto, il metodo di diagnostica basato sul segnale di tensione di cui sopra potrebbe non essere in grado di rilevare tempestivamente un leggero allentamento del collegamento.
3 L'impatto delle vibrazioni
Eseguire test di carica e scarica a pressione atmosferica su batterie sottoposte a trattamento con vibrazioni a bassa tensione, per dimostrare i cambiamenti nelle prestazioni di carica e scarica delle batterie al litio dopo il trasporto aereo. I risultati hanno mostrato che dopo il trattamento con frequenza di vibrazione a 60 Hz e 80 Hz in un ambiente a bassa tensione, l'effetto di carica è stato inferiore a quello della batteria originale e il trattamento a 60 Hz ha avuto l'impatto più significativo sulla capacità delle batterie al litio;
Le altre frequenze di vibrazione accelerano tutte la velocità di carica e la variazione è significativa a 120 Hz. Durante il processo di scarica, la curva delle batterie al litio con trattamento di vibrazione a 120 Hz presenta la deviazione maggiore, mentre quella con 200 Hz presenta la deviazione minore. Le altre deviazioni variano da piccole a grandi, tra cui 60 Hz, 80 Hz, 180 Hz, 160 Hz, 140 Hz e 100 Hz.
È stato riscontrato che non esiste una correlazione positiva tra la frequenza di vibrazione e la situazione di scarica, il che potrebbe indicare che il danno alla struttura causato dalle vibrazioni è legato alla reattività della struttura stessa della batteria alla frequenza e all'ampiezza. Alcune frequenze e ampiezze di vibrazione danneggiano maggiormente la struttura delle batterie al litio 18650.
Dal confronto complessivo delle curve di carica e scarica, si può notare che la capacità di scarica di tutte le batterie sottoposte a vibrazioni è inferiore a quella della batteria originale e la velocità di scarica è più rapida di quella della batteria originale. Ciò può indicare che la capacità e le prestazioni di scarica della batteria saranno danneggiate dalle vibrazioni meccaniche.
Infatti, dopo essere state sottoposte a vibrazioni meccaniche, il grado di contatto tra gli elettrodi positivi e negativi nell'elettrolita delle batterie agli ioni di litio si modifica, con conseguente variazione dell'area di contatto tra l'elettrodo e la soluzione elettrolitica, che ostacola il trasferimento degli ioni di litio all'elettrodo negativo durante la carica e la scarica, riducendo così la quantità di litio incorporata nell'elettrodo negativo.
4 Conclusioni
Questo articolo propone un metodo di diagnosi dei guasti per le connessioni dei pacchi batteria agli ioni di litio basato sui segnali di vibrazione meccanica e giunge alle seguenti conclusioni. L'utilizzo di diversi fogli ceramici piezoelettrici per generare l'eccitazione delle vibrazioni, misurare la risposta alle vibrazioni ed estrarre le caratteristiche di tempo-frequenza dal segnale di risposta può raggiungere efficacemente la classificazione delle modalità di guasto delle connessioni a punto singolo e multipunto. Il lavoro futuro prevede l'ottimizzazione della disposizione dei fogli ceramici piezoelettrici, la raccolta dei segnali di vibrazione dall'ambiente del veicolo e l'adattamento di questo metodo alla diagnosi dei guasti di connessione dei pacchi batteria agli ioni di litio nei veicoli