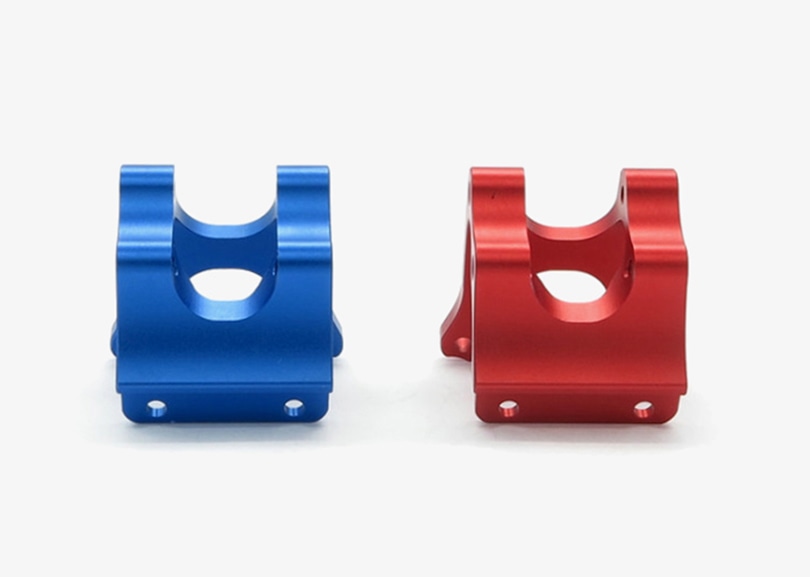
#News
Trattamento superficiale: processo di anodizzazione
L'anodizzazione è un processo di passivazione elettrolitica utilizzato per aumentare lo spessore dello strato di ossido naturale sulla superficie delle parti metalliche.
Il processo è chiamato anodizzazione perché la parte da trattare forma l'elettrodo anodo di una cella elettrolitica.
L'anodizzazione aumenta la resistenza alla corrosione e all'usura e fornisce una migliore adesione per primer e colle per vernici rispetto al metallo nudo. Le pellicole anodiche possono essere utilizzate anche per diversi effetti cosmetici, sia con rivestimenti porosi spessi che possono assorbire coloranti o con rivestimenti trasparenti sottili che aggiungono effetti di interferenza delle onde luminose riflesse.
L'anodizzazione viene utilizzata anche per prevenire il grippaggio dei componenti filettati e per realizzare pellicole dielettriche per condensatori elettrolitici. I film anodici sono più comunemente applicati per proteggere leghe di alluminio, sebbene esistano anche processi di titanio, zinco, magnesio, niobio, zirconio, afnio e tantalio. Il metallo di ferro o acciaio al carbonio si esfolia quando viene ossidato in condizioni microelettrolitiche neutre o alcaline; cioè, l'ossido di ferro (in realtà idrossido di ferro o ossido di ferro idrato, noto anche come ruggine) si forma da fosse anodiche anossiche e una grande superficie catodica, queste fosse concentrano anioni come solfato e cloruro accelerando il metallo sottostante alla corrosione. Scaglie o noduli di carbonio in ferro o acciaio ad alto contenuto di carbonio (acciaio ad alto tenore di carbonio, ghisa) possono causare un potenziale elettrolitico e interferire con il rivestimento o la placcatura. I metalli ferrosi sono comunemente anodizzati elettroliticamente in acido nitrico o mediante trattamento con acido nitrico fumante rosso per formare ossido di ferro nero duro (II, III). Questo ossido rimane conforme anche quando placcato sul cablaggio e il cablaggio è piegato.
L'anodizzazione modifica la struttura microscopica della superficie e la struttura cristallina del metallo vicino alla superficie. I rivestimenti spessi sono normalmente porosi, quindi spesso è necessario un processo di sigillatura per ottenere resistenza alla corrosione. Le superfici in alluminio anodizzato, ad esempio, sono più dure dell'alluminio ma hanno una resistenza all'usura da bassa a moderata che può essere migliorata con l'aumentare dello spessore o applicando sostanze sigillanti adeguate. I film anodici sono generalmente molto più resistenti e aderenti della maggior parte dei tipi di vernice e placcatura metallica, ma anche più fragili. Ciò li rende meno soggetti a crepe e desquamazione a causa dell'invecchiamento e dell'usura, ma più suscettibili alle crepe dovute allo stress termico.