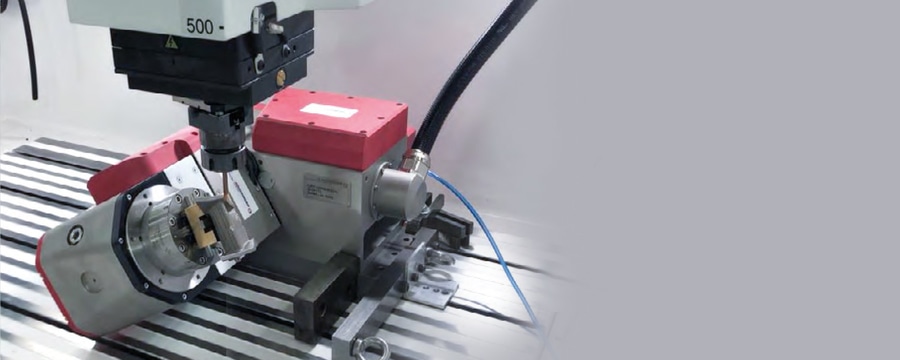
#News
FORATURA DI FORI DIFFUSORI nelle pale delle turbine
La strategia di business di ONA nel settore aeronautico prevede in gran parte la fornitura alle aziende di soluzioni personalizzate ad alto valore aggiunto.
Un esempio è stato lo sviluppo di un'applicazione personalizzata per un importante produttore di componenti di alta qualità utilizzati nei settori aerospaziale ed energetico. Il loro bisogno di prodotti di così alta qualità è stato un fattore chiave nella loro decisione di optare per ONA.
Il cliente richiedeva una soluzione per la perforazione dei fori del diffusore nelle pale delle turbine. Questi fori svolgono un ruolo importante nella ventilazione e nel raffreddamento. Una scarsa ventilazione e raffreddamento aumentano la temperatura di ingresso dell'aria della turbina e, infine, riducono l'efficienza e la durata del componente. In una turbina di generazione di energia, verrebbe prodotta meno energia e in una turbina di propulsione (come una turbina per aeroplani) verrebbe consumato più carburante. Inoltre, le alte temperature possono anche danneggiare le stesse pale del compressore.
I fori nelle lame vengono normalmente lavorati utilizzando il nostro macchinario FAST HOLE (FH) che utilizza una tecnologia specializzata per velocità di lavorazione più elevate. Tuttavia, i requisiti di alta precisione e qualità del produttore per la perforazione dei fori (con diverse forme geometriche: conica, trapezoidale, ecc.) Non potevano essere soddisfatti dalle nostre apparecchiature FH, quindi hanno chiesto a ONA di fornire una soluzione specifica a questo problema.
La proposta dei nostri ingegneri era di sviluppare un'applicazione che combinasse le capacità di due tecnologie di elettroerosione: FAST HOLE e die sink EDM. Dapprima si praticano fori cilindrici nel pezzo mediante una macchina FH e poi, utilizzando una macchina ONA IRIS6 (percorsi degli assi XYZ: 1000 x 750 x 650 mm; con tavola rotante a 2 assi ed elettrodo in rame), altri anche nei primi fori vengono praticati fori con le forme geometriche richieste. L'asse di alcuni di questi fori potrebbe non essere parallelo all'asse del primo foro.
Come siamo riusciti a farlo
Una delle difficoltà nell'attuazione di questo progetto era la situazione globale dell'epoca. Trovandoci nel mezzo della pandemia di Covid, gli incontri faccia a faccia tra il team di ONA e il cliente erano impossibili. Questa sfida è stata vinta grazie all'ottima collaborazione tra i diversi reparti di ONA e alla nostra competenza digitale, che ci ha permesso di inviare eventualmente una gara telematica al cliente finale.
1. Studio di fattibilità e valutazione della qualità finale.
In primo luogo, è stato condotto uno studio di fattibilità e valutazione finale della qualità per verificare se il test potesse essere eseguito utilizzando una macchina ONA. Questa simulazione è stata effettuata in Cina su una macchina nello showroom della filiale.
2. Idoneità della macchina ONA IRIS6.
Una delle conclusioni di questo studio preliminare di fattibilità è stata l'idoneità della macchina ONA IRIS6 date le caratteristiche del progetto: le dimensioni dei pezzi e la necessità di una tavola rotante per eseguire tutti i fori e poter ruotare il pezzo. Nel caso dell'elettrodo, abbiamo deciso di utilizzare il rame per ottenere una finitura di qualità superiore.
3. Offerta in video.
Vista la situazione della pandemia, i limiti imposti e l'interesse mostrato dal cliente nel voler portare avanti il progetto, ONA ha presentato la gara in video, esprimendo la nostra totale fiducia nella qualità del pezzo finale.
4. Visualizza e collega con CAD-CAM il nuovo CNC.
Il cliente ha chiesto di mostrare il nuovo software CNC e come si collega al CAD/CAM. ONA utilizza entrambi i sistemi software per ottenere il miglior abbinamento, in modo che il pezzo “ideale” creato dal software CAD/CAM venga elaborato dal CNC della macchina e il risultato finale sia una replica esatta di quanto progettato. In questo caso particolare, era molto importante individuare i fori già praticati, determinare le coordinate esatte in tempo reale e assicurarsi che la macchina fosse in grado di eseguire l'operazione nel punto esatto. La messa a punto del pezzo è stata fondamentale, oltre a poterlo posizionare nel punto esatto, in quanto la forma dei pezzi era molto complessa.
5. Programmazione con ONA Script.
Infine, la programmazione è stata eseguita utilizzando il nostro strumento software ONA Script, un generatore di flusso di lavoro che consente alla macchina di eseguire l'intero processo senza interruzioni.
Nel caso di questo particolare compito, si trattava di un progetto chiavi in mano che prevedeva un alto livello di collaborazione con il cliente in ogni momento. Ciò ha reso più facile raggiungere con successo l'obiettivo finale della produzione diretta di una parte.
Conclusioni
Come risultato di tutto questo duro lavoro e di studi precedenti, siamo stati in grado di fornire al cliente una macchina per elettroerosione a tuffo completamente personalizzata programmata in base alle sue esigenze specifiche per la lavorazione di fori diffusori con geometria complessa nelle pale delle turbine. Come ci ha informato il cliente, la nostra soluzione chiavi in mano era anche più conveniente rispetto ad altre alternative sul mercato.
La macchina ONA IRIS6 incorpora un generatore digitale intelligente, un'innovazione tecnologica rivoluzionaria nella tecnologia EDM. È il 30% più potente di altri generatori più avanzati. Può raggiungere fino a 400 ampere, quattro volte più potente del generatore standard, ed è progettato per ottimizzare il processo di elettroerosione a tuffo controllando l'apporto di energia di ciascuna scarica, riducendo così l'usura degli elettrodi fino al 500%.