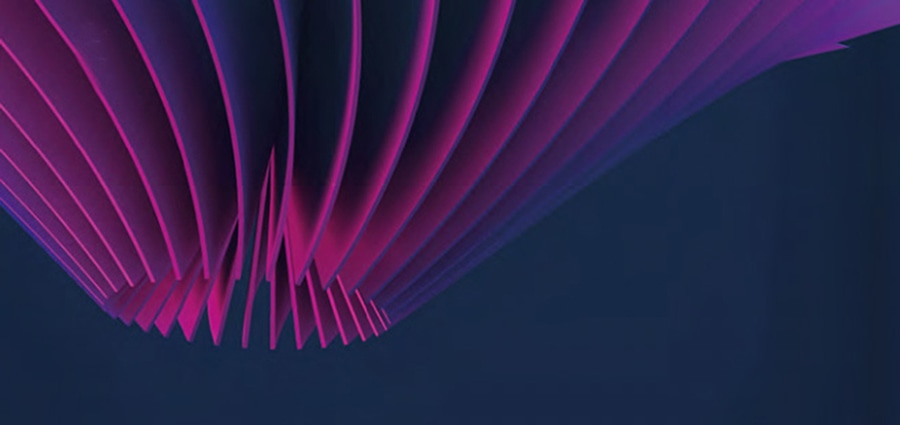
Vedi traduzione automatica
Questa è una traduzione automatica. Per vedere il testo originale in inglese cliccare qui
#News
Lavorazione a scarica elettrica (EDM) di giranti di turbine per compressori industriali
Due dei punti di forza dell'ONA nell'industria della produzione di componenti per turbine si basano sulla nostra competenza nella lavorazione a scarica elettrica (EDM) di parti altamente complesse, nonché su oltre 25 anni di esperienza nella fornitura di soluzioni chiavi in mano per le turbine.
Questa leadership di mercato e le conoscenze specialistiche hanno portato una delle aziende di riferimento nella produzione di pompe e valvole a riporre la propria fiducia in ONA per lo sviluppo delle giranti per le sue apparecchiature rotanti.
L'elettroerosione è l'opzione più efficiente e praticabile per la lavorazione di parti con geometrie complicate, come le cavità delle giranti. Ciò è dovuto al fatto che la tecnologia dell'elettroerosione supera le difficoltà presentate da altre tecniche tradizionali, come la fresatura, che spesso porta ad alti tassi di rottura degli utensili o, soprattutto nel caso di geometrie chiuse o complesse come le giranti, all'impossibilità per gli utensili di fresatura di raggiungere tutte le aree da lavorare.
Tuttavia, se da un lato la lavorazione a scarica elettrica è il metodo più fattibile per fornire una soluzione ottimale di erosione e lavorazione, dall'altro pone delle sfide importanti: L'elettroerosione comporta la considerazione di diversi fattori complicati, come il design e il numero di elettrodi necessari, la loro traiettoria, il livello di usura e così via, il cui calcolo e definizione devono essere attentamente considerati.
Per rispondere a queste sfide, il nostro team di ingegneri ha sviluppato una "soluzione chiavi in mano" che risponde a tutte le esigenze del cliente. A tal fine, ha studiato e valutato il caso specifico in dettaglio, sviluppando con successo l'applicazione su misura per la lavorazione delle giranti, il "cuore" delle turbine, che sarebbero state utilizzate dal nostro cliente per la generazione di energia elettrica, il pompaggio e la movimentazione di fluidi industriali.
Come siamo riusciti a farlo
Sulla base dei disegni forniti dal cliente e delle esigenze espresse, il team ONA ha valutato l'opportunità di utilizzare la tecnologia di elettroerosione a tuffo per la lavorazione di parti geometricamente complicate come le giranti.
1. Layout.
In questa fase iniziale è stato fondamentale definire correttamente gli assi coinvolti nel processo, nonché la posizione e l'orientamento del pezzo, poiché entrambi i fattori influenzano in modo significativo la progettazione e la traiettoria degli elettrodi, le dimensioni della lavorazione e possono persino compromettere la fattibilità del progetto stesso.
2. Progettazione e traiettoria degli elettrodi
Attualmente non è disponibile sul mercato un software CAD/CAM commerciale in grado di determinare la progettazione e la traiettoria degli elettrodi come nel caso di altre applicazioni, per cui è necessario ricorrere a conoscenze specialistiche per sviluppare algoritmi e metodologie ad hoc per definire tali parametri. Ciò significa che non esiste un'unica soluzione, ma che ogni pezzo richiede un progetto personalizzato in base alle sue particolari caratteristiche ed esigenze.
3. Lavorazione degli elettrodi.
Le sfide legate alla lavorazione e alla fresatura degli elettrodi hanno a che fare principalmente con le loro geometrie complesse e la necessità di tolleranze molto strette; ciò significa che un errore nell'elettrodo comporta un errore nel pezzo.
4. Parametri dell'elettroerosione.
Per una lavorazione stabile del pezzo, i diversi parametri dell'elettroerosione devono essere definiti correttamente. Questi parametri sono definiti principalmente dalla rugosità superficiale richiesta (minore è il tempo di lavorazione, maggiore è la rugosità) e dalla geometria (aree più grandi consentono di applicare più energia).
5. Usura dell'elettrodo.
L'usura è una conseguenza inevitabile del processo di elettroerosione; non può essere evitata, ma può essere controllata e minimizzata.
6. Metrologia
Data la difficoltà di accedere al pezzo stesso, l'analisi dimensionale del pezzo in questione è di per sé una sfida; pertanto metodi come l'analisi distruttiva, la definizione di punti strategici o l'utilizzo di elementi di misura standard sono alcune delle possibilità da considerare in questo caso.
LA SOLUZIONE ONA: come l'abbiamo ideata
Per superare con successo tutte le sfide che questo progetto comportava, era indispensabile avvalersi di un team di ingegneri come quello di ONA, esperti nella tecnologia dell'elettroerosione.
Dopo uno studio preliminare approfondito del pezzo e dei suoi diversi parametri, e dopo aver valutato la fattibilità del progetto, la proposta dei nostri ingegneri è stata quella di sviluppare un'applicazione per la nostra macchina per elettroerosione a tuffo IRIS 6+. Questa apparecchiatura, tra gli altri vantaggi, offre la massima precisione di elettroerosione e livelli di produttività elevati
Oltre alla scelta del macchinario più adatto, lo sviluppo completo dell'applicazione finale da parte di ONA ha incluso parametri critici come la definizione degli elettrodi necessari e l'analisi della loro usura. Nel caso di questo progetto, l'applicazione richiedeva 4 elettrodi diversi per ottenere traiettorie complete. Questo è anche uno dei vantaggi competitivi dell'ONA in termini di ottimizzazione dei tempi. Sebbene l'usura degli elettrodi sia inevitabile, la tecnologia incorporata nel generatore digitale 100% intelligente di ONA IRIS riutilizza gli elettrodi e ne riduce l'usura.
Allo stesso modo, il team di ingegneri ha sviluppato la traiettoria tridimensionale (curve, inclinazioni...) che la nostra macchina deve seguire per eseguire correttamente l'intero processo e, dove necessario, è stato implementato uno strumento di serraggio personalizzato per posizionare correttamente il pezzo.
Conclusioni
- ONA dimostra la sua capacità di affrontare progetti integrali chiavi in mano.
- Sviluppo di un'applicazione personalizzata per la produzione di un pezzo molto complesso in termini di forma, accesso e cavità.
- Un chiaro esempio di potenziale tecnologico e di competenza nell'elettroerosione.
- Precisione e affidabilità delle macchine IRIS per la lavorazione di pezzi critici e complessi.
- ONA come partner tecnologico specializzato in settori come la produzione di componenti per turbine. In questo caso particolare, l'attenzione è rivolta alla lavorazione delle giranti, ma qui potete leggere un altro caso di studio relativo alla nostra soluzione personalizzata per la lavorazione dei fori dei diffusori nelle pale delle turbine.
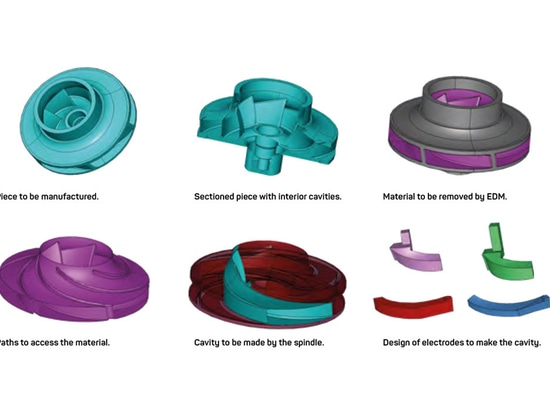
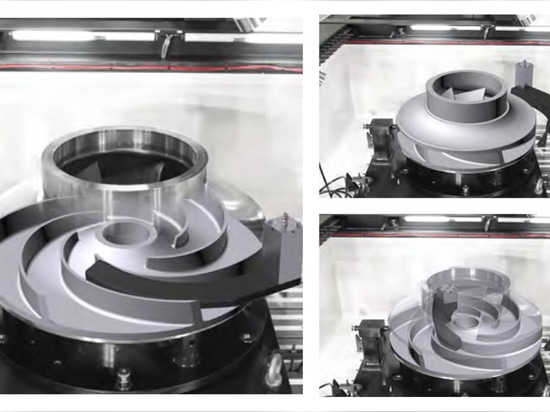