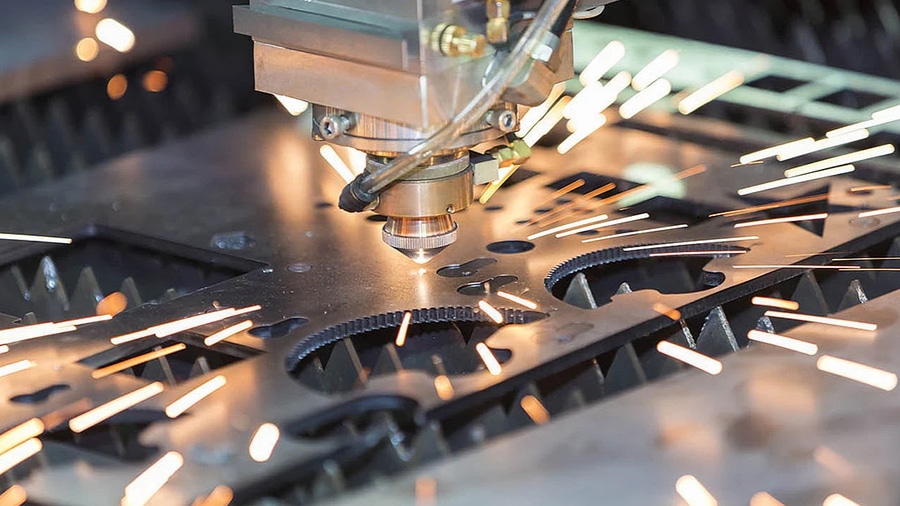
Vedi traduzione automatica
Questa è una traduzione automatica. Per vedere il testo originale in inglese cliccare qui
#News
Metodi di taglio Parte 1: Taglio laser
Tra i metodi di lavorazione della lamiera, il taglio laser è relativamente nuovo, eppure ha conquistato il settore. Con questo metodo di lavorazione iniziamo la nostra nuova serie sui processi di taglio e il loro impatto sui processi a valle.
Il taglio laser si è affermato nella lavorazione della lamiera, soprattutto per i materiali più sottili. Il motivo: a differenza della punzonatura o della cesoiatura, il laser è uno strumento eccezionalmente flessibile. Questo significa che il taglio laser è spesso conveniente a partire dal lotto 1. Molte commesse si sono specializzate in questo processo, perché consente loro di produrre nuovi pezzi per i vari clienti in modo semplice.
Una luce speciale consente il taglio laser
Il termine laser (composto dalle parole "light amplification by stimulated emission of radiation") si riferisce sia al raggio che al dispositivo utilizzato per generare i raggi laser. Il raggio laser utilizzato per il taglio è quindi un'onda elettromagnetica. Queste onde si differenziano dalla luce ordinaria per diversi fattori: elevata intensità, intervallo di frequenza spesso molto ristretto (luce monocromatica), netto raggruppamento del fascio e grande coerenza (le onde hanno una relazione di fase fissa nella propagazione spaziale e temporale). Un raggio laser può riscaldare e ablare quasi tutti i materiali, il che in fisica si chiama ablazione.
I laser sono spesso denominati in base alle proprietà del loro mezzo ottico laser, cioè il materiale che genera la luce laser. Importanti per la lavorazione della lamiera sono soprattutto il laser CO2 con mezzo laser gassoso e il laser a fibra, che lavora con fibre di vetro.
Il taglio laser consiste in due operazioni
In senso stretto, durante il taglio laser avvengono contemporaneamente due processi: In primo luogo, il materiale sul fronte di taglio assorbe il raggio laser e si riscalda. In secondo luogo, il gas di soffiaggio soffia il materiale ablato fuori dal taglio, proteggendo così anche le ottiche di messa a fuoco da vapori e spruzzi.
A seconda che il materiale venga rimosso dal taglio come liquido, prodotto di ossidazione o vapore, si distingue tra taglio a fusione con raggio laser, taglio a fiamma con raggio laser e taglio a sublimazione con raggio laser.
Il taglio laser può anche rendere necessaria la sbavatura
Ciò ha conseguenze anche sulla formazione di bave. È vero che i pezzi realizzati al laser in acciaio dolce e acciaio inossidabile possono risultare privi di bave, a seconda dello spessore e della complessità del contorno. Per questo, tuttavia, l'ottica di messa a fuoco e i parametri di processo devono essere impostati in modo ottimale. Più i pezzi sono spessi, tuttavia, maggiore è la perdita di fusione. Anche i contorni stretti possono rendere necessaria una rilavorazione. La formazione di bave è inevitabile nei pezzi di alluminio tagliati al laser.
Nel caso dei laser piani, si verificano adesioni anche sul lato inferiore della lastra a causa dei riflessi della griglia di supporto. Questo fenomeno non può essere evitato anche se tutti i parametri sono perfettamente adattati. Nel caso del taglio laser a fiamma, i bordi tagliati presentano anche uno strato di ossido dopo il processo, che deve essere rimosso.
Il taglio laser funziona con acciaio fino a uno spessore di circa 40 mm, con acciaio inossidabile fino a circa 50 mm e con alluminio fino a 25 mm. L'alluminio, tuttavia, è un materiale difficile da tagliare perché riflette la maggior parte delle radiazioni laser e perché la sua elevata conducibilità termica dissipa molta energia dalla fessura di taglio. Lo stesso vale per il rame.
L'arrotondamento dei bordi dopo il taglio laser è un must
Anche i pezzi tagliati perfettamente vengono spesso rilavorati con una sbavatrice, perché un taglio laser ha bordi molto taglienti. Questo è ancora più vero per i laser a fibra che per i laser a CO2. Poiché molti clienti desiderano non solo sbavare ma anche arrotondare i bordi, questa fase del processo è assolutamente necessaria.