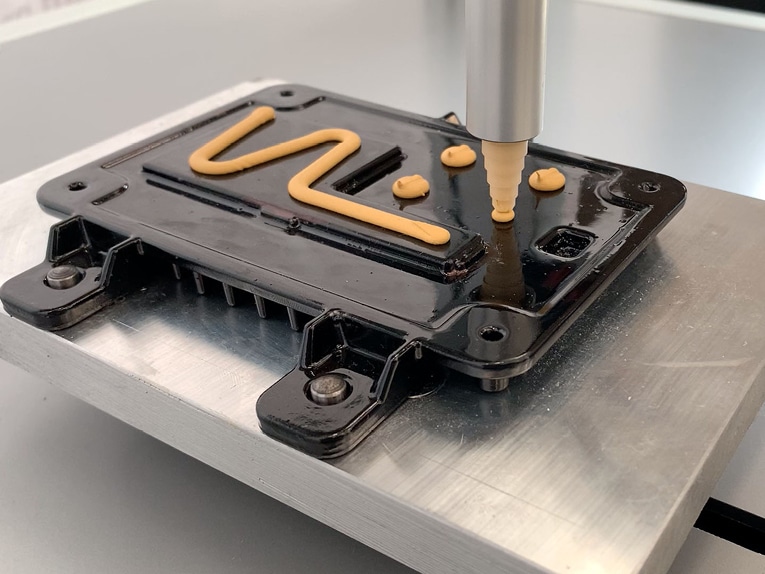
#Tendenze
GAP FILLER e Paste Termo-conduttive
Processo di Thermal Management: uno degli argomenti più discussi e sviluppati!
La continua evoluzione della tecnologia e la sua “elettrificazione” ha scaturito negli ultimi anni la necessità di prestare alcune accortezze che possano garantire la lunga durata dei componenti; tra queste, il processo di Thermal Management è sicuramente tra i più discussi e sviluppati.
A questo proposito la dispensazione di paste termo-conduttive, conosciute anche come gap filler, ha acquisito sempre più importanza in processi di assemblaggio di componenti elettrici ed elettronici. Sappiamo infatti che la corrente elettrica, sia questa di alimentazione o generata per trasferimento di dati, genera calore; è chiaro che la miniaturizzazione dei componenti elettronici e le elevate velocità dei processori odierni hanno inevitabilmente portato la necessità di disperdere il calore generato per evitare il surriscaldamento locale dei componenti elettronici coinvolti, ergo salvaguardarne l’integrità. Basti pensare allo sviluppo dei veicoli elettrici, dove è necessario poter controllare l’alta temperatura generata dalle prestazioni di ricarica e dall’elevata tensione di lavoro.
I materiali termo-conduttivi vengono quindi dispensati a contatto con i componenti per consentire la dissipazione del calore generato, e in secondo luogo per compensare eventuali giochi, tolleranze/vuoti d’aria che si creano nel processo di assemblaggio di questi componenti; grazie alla loro consistenza morbida e flessibile permettono infatti di proteggere i componenti anche da urti o vibrazioni.
Generalmente parlando, i gap filler sono costituiti da materiale polimerico, siliconico o epossidico, combinato con particelle solide appunto termo-conduttive e che non conducono elettricità; ecco allora che possiamo trovare paste a base metallica, a base ceramica o a base carbonica con polvere di diamante o delle fibre in carbonio, che rendono spesso questi fluidi parecchio costosi.
Questo porta inevitabilmente delle criticità nella dispensazione di questi materiali, data la natura altamente abrasiva di queste paste che si presentano sia in forma mono-componente, sia in forma bi-componente.
Ecco perché la soluzione firmata Dav tech rappresenta una svolta per la loro corretta dosatura. Le pompe volumetriche per mono-componente PCP e quelle per bi-componente PDP sono infatti la perfetta soluzione in termini di performance e durabilità. Il principio della pompa monovite a cavità progressiva, la possibilità di dispensare cordoli piuttosto che punti, e la possibilità di scegliere rotori in carburo di tungsteno o ceramica per resistere all’abrasività, invece che in acciaio inox, identificano una soluzione solida, affidabile e senza pari.
Attenzione però che anche nella scelta del gruppo di alimentazione, bisogna essere accorti e non sottovalutare le criticità che si presentano sia in fase di dispensazione, sia in fase di alimentazione prodotto; ecco perché dove le quantità lo richiedono (laddove una cartuccia pressurizzata – tipo Semco - non bastasse), la soluzione che Dav tech accompagna alle pompe PCP / PDP è rappresentata dalle pompe di alimentazione elettriche PPE / PPE2K (nel caso di bi-componenti), che lavorano sempre tramite il principio della pompa a cavità progressiva, gestite da un motore elettrico ad anello chiuso, servo controllato, che ne permette una retro-azione elettrica appunto controllata. Il risultato è un pompaggio di prodotto privo di picchi di pressione, che tendenzialmente provocherebbero stress al prodotto stesso, favorendo il fenomeno di separazione del gap filler proprio in virtù della presenza delle particelle solide termo-conduttive.
La possibilità di poter controllare la velocità del suo motore elettrico, permette alla pompa PPE / PPE2K di gestire un pompaggio costante e privo di picchi, che se associato alle caratteristiche peculiari delle pompe di dosaggio volumetrico PCP / PDP, garantisce il perfetto controllo del processo di Thermal Management nelle applicazioni di assemblaggio.